With the continuous development of electronic technology, motor protectors are moving in the direction of intelligence, digitization, and integration. At present, most of the conventional integrated motor protectors on the market have relatively complete protection functions, but they are bulky, inconvenient to install, and expensive, which makes the promotion of integrated motor protectors greatly limited. In the mining site, subject to field space constraints, and only need basic motor protection functions, in order to solve the above problems, it is necessary to develop a motor protector that meets national standards and is cost-effective. This article uses ARM as the processor, has developed a economical and practical simple low-voltage motor protector.
1, design basis and function
The simple low-voltage motor protector includes the following functions:
(1) Basic protection functions: protection functions such as phase failure, start-up timeout, inverse time overload, grounding, three-phase unbalance, locked rotor, blocking, short-circuit, over-voltage, etc., and comply with GB14048.4, GB14048.6 and other standards.
(2) Matching protection function: optional protection functions such as external fault, leakage, time-limited overload, underload, undervoltage, etc., which meet the standards of GB14048.4 and GB14048.6.
(3)Measurement and communication functions: Measure three-phase current, residual current, three-phase voltage; RS485 communication interface, Modbus communication protocol, communication conforms to GBZ19582.1, GBZ19582.2 standard.
(4) DI/DO, transmission output function: Supports 2-way DI and 4-channel DO; Supports 1-channel 4-20mA transmission output.
(5) Installation method: Use rail mounting or screw mounting. The three kinds of rated current specifications are 5A, 25A and 100A, respectively.
2, hardware solutions
A simple motor protector adopts a low-cost design scheme. The entire system consists of a central processing unit, a power supply module, a signal processing unit, a button module, a display module, an I/O control module, a transmission output module, a communication module, etc., and the system hardware structure. As shown in Figure 1. The signal processing unit and control module are highlighted.
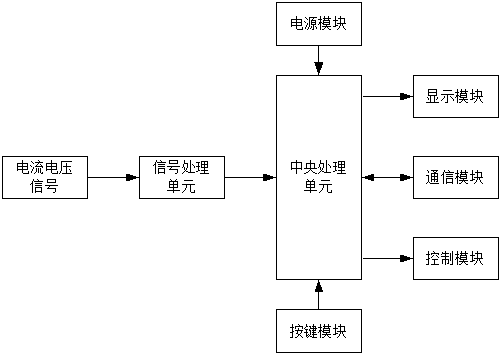
Figure 1 system hardware structure
2.1 Signal Processing Unit
The signal processing unit circuit is shown in FIG. 2 , and the signal detected by the sensor is raised by the reference voltage signal Vref, is limited to a signal of 0 to 3.3V, and is input to a central processing unit to achieve AC sampling. In order to ensure the accuracy of AC sampling, a method of dividing the AC signal is adopted. When a large signal is input, the signal is directly filtered and then directly into the CPU for sampling processing. When a small signal is input, the signal needs to pass through an operational amplifier after being raised. After amplification and filtering, enter the CPU for sampling processing.
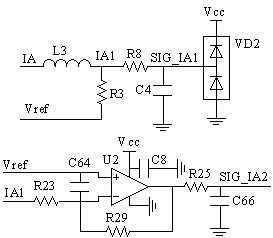
Figure 2 signal processing unit circuit
2.2 Control Module
The control module consists of digital inputs and relay outputs. The digital input uses the internal 15V power supply provided by the protector and uses optocoupler isolation to enhance the anti-interference of the digital input and meet the requirements of the power frequency withstand voltage of the protector. The digital input is used for monitoring the external switch status. Relay output uses a relay with stable and reliable performance and long service life. Relay output circuit diagram shown in Figure 3, in order to enhance the anti-jamming requirements, the use of optocoupler isolation, ULN2003A can output 500mA current, can withstand 50V voltage, internal integrated freewheeling diode for the moment when the relay coil power off higher The freewheeling circuit is provided by the inductive voltage. The relay output is used for output of signals such as fault tripping, fault alarm and remote start.
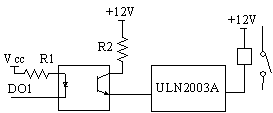
Figure 3 relay output circuit
3, software program
The main flow chart of the protector is shown in Fig. 4. It mainly includes A/D sampling, calculation display, basic protection, key processing, I/O control, transmission output and communication. The main program adopts a modular design and features high portability.
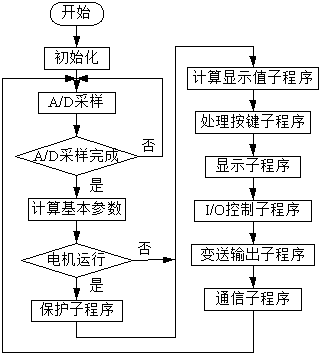
Figure 4 main program flow
After the main program is initialized, the A/D sampling program is executed. In the A/D sampling procedure, the three-phase current, three-phase voltage and residual current of the motor are sampled. After the sampling period is over, the current of the motor is calculated based on the three-phase current value, three-phase voltage value, and residual current value obtained by sampling. The value and voltage value are then used to determine the current motor operating state. When the motor is in the operating state, the motor protection subroutine is executed.
In the protection subroutine, according to the voltage value of the current value obtained by the sampling calculation, it is judged whether the motor has a fault. If no fault occurs, the main routine is returned. If any fault occurs, it is determined which type of motor fault has occurred and the corresponding fault processing is performed. , and the fault type is displayed on the protector interface.
After the protection subroutine is executed, it enters the display value calculation subroutine to calculate the display values ​​of three-phase current, average current, three-phase voltage and residual current. After the display value calculation subroutine is executed, enter the key processing subroutine to realize human-computer interaction.
After the key processing subroutine is executed, enter the display subroutine. When there is no key processing, the current average current value of the motor is displayed; when there is key processing, the parameter value corresponding to the key function is displayed. When the motor fails, the corresponding fault code and the fault alarm trip lamp are displayed.
After the display subroutine is executed, it enters the I/O control program. When the motor fails, the control relay outputs the normally closed contact to open and close, and the motor is cut off to stop the motor. After the I/O control program is executed, it enters the subroutine for transmission and output. It can select any of the three-phase current, average current, three-phase voltage, and frequency to be converted into 4~20mA analog signal output.
After the transmission output subroutine is completed, it enters the communication subroutine. Firstly, it is judged whether the command data sent by the upper computer is received. After receiving the command data, it is determined whether the address code in the command is the protector local address according to the standard Modbus protocol. If the address is the local address, the upper computer sends back the corresponding parameter data.
4, application examples
Due to the complexity of the cement production process and the large number of motor units in a cement plant, a simple motor protector is used to effectively protect the on-site motor equipment. This not only enables the motor to fully exert its overload capacity, but also improves the reliability of the electric drive system. And the continuity of the production process. The cement plant uses protectors for motor protection and control circuits, replaces thermal relays as overload protection and control elements for motors, and uses communication technology to automate the control of motor equipment in cement production, making the motor of large-scale cement plants effective. Protection and control.
5 Conclusion
With the application of motor protectors, the market demand for products is constantly changing. For the market demand for economical motor protectors, a simple and economical motor protector was developed. The simple protector is an intelligent, digital motor protector with ARM as the core. When the motor starts with overtime, overload, phase failure, underload, imbalance, stall, blocking, short circuit, overvoltage, undervoltage, etc. Real-time protection ensures that industrial equipment can operate safely and reliably.
Source: "Electrical Age" 2017 issue 12.
references
[1] Huang Kai, Liu Xiangjun. Development and prospect of motor protectors [J]. Electrical Technology. 2017,(3):1-4
[2] Wang Xin. Low-voltage automatic motor integrated protector based on PIC single-chip microcomputer[J]. Mechatronic Engineering Technology. 2016,(10):30-31,102
[3] Sun Xiuzhen. Research on intelligent protection of motor with STC12C5410 MCU[J]. Industrial and Information Education. 2013,(2):91-94
[4] Zhao Bo, Hu Jingtai, Huang Wentao. Design Principle of ARD3T Smart Motor Protector Body and Measurement Module[J]. Power System Protection and Control. 2012,(12):136-140
[5] Zhao Bo, Wu Jianming, Tang Jianjun. Motor Protector Based on H8/3687FP Microcontroller[J]. Low Voltage Apparatus. 2007,(19):25-27
Custom Camlock,Brass Industrial Hose Coupling,Aluminium Camlock Type Dc,Adaptor Hose Shank
SHIJIAZHUANG STRONGFLEX I/E CO.,LTD. , https://www.sjzhydraulichose.com