Model NO.: GX-105/120
Working Efficiency: 3-8 Second One Cycle
Warranty: 4 Years
Plastic: Polystyrene GPPS
Mateiral: PS Foam Sheet
Automatic: Automatic with Robot Arm
Forming Size: 1100mm*1250mm
Installation Power: 120kw
Forming Depth (Max.): 130mm
Transport Package: Wood and Iron Framework
Origin: China
HS Code: 8474809090
Model NO.: GX-105/120
Working Efficiency: 3-8 Second One Cycle
Warranty: 4 Years
Plastic: Polystyrene GPPS
Mateiral: PS Foam Sheet
Automatic: Automatic with Robot Arm
Forming Size: 1100mm*1250mm
Installation Power: 120kw
Forming Depth (Max.): 130mm
Transport Package: Wood and Iron Framework
Origin: China
HS Code: 8474809090
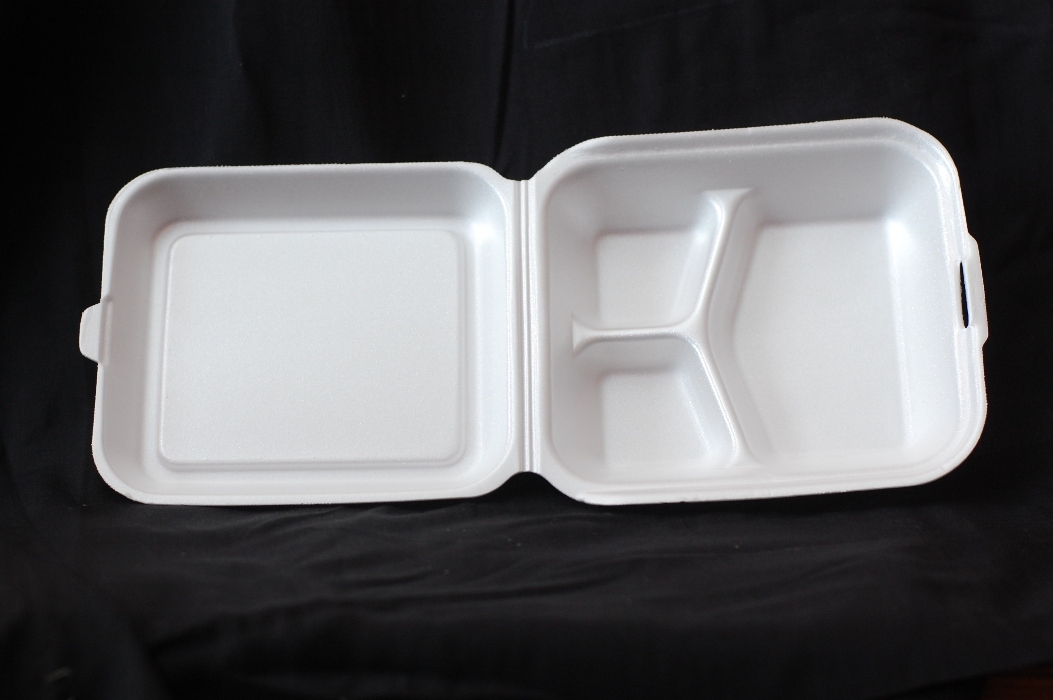
PS foam food box making machine, use the PS foam sheet made by the PS foam sheet extruder, as the materials.
throught changing the different molds to get the various kinds of colorful products, like the PS foam food box, PS foam food tray, egg tray, bowl, cake case, fruit tray, and absorbent tray to contain the meat, or fish or shrimp,etc,.
which is used for package industry.
Â
GENERAL INFORMATION:
Â
Â
Â
Raw material:Â |
PS granule, talc, butane and so on.   |
Finished products:Â |
Ps foam fast food box, foam tray, pizza box, hamburger, egg tray, and so on. (Depending on changing mold)Â Â Â Â |
Sheet thickness: |
1-5mm |
Sheet width:Â |
600-1200mm |
Capacity:Â Â |
180-240kgs/h |
Operator: |
6-8 workers |
Water consumpation:Â |
200kgs/24hrs |
Cooling water tower:Â |
20 T/ h |
Butangas consumption:Â |
45-50 kgs/one ton materials (based on the foam ratio range from 16-20) |
Air compressor : |
1.5 m3/min |
Installation power: |
550Kw |
Power supply : |
3 phase 4 line 380V 50Hz |
Work shop area:Â |
PS Foam Sheet Extrusion Line workshop: 25x8x4m (L*W*H) Fully-automatic Vacuum Forming Machine workshop :20x8x4m  |
Warehouse: |
Per raw material warehouse area 60M2 (at least) Per finished products warehouse area 60M2 (at least) Â |
Container |
3x 40'HQ containers |
Each factory has its respective advantage about what they done , and each manufacturer is good factory, which is the truth, and we believe it.
While here is us , Yantai gossie be your nice choice.
Â
Main equipment and technical parameter
1). GX- 105/120 PS Foam Sheet Extrusion Line
1). GX- 105/120 PS Foam Sheet Extrusion Line
Components: |
 |
A.Mixer |
 |
Hopper Capacity |
300-500kg/ hopper (controlled by time relay) |
Motor |
1 set, 4-pole, 3kw |
B. Automatic Feeding System |
 |
Automatic Self-control System |
 |
Motor |
1 set, 6-pole, 1.1kw |
C. NO.1 Extruder |
 |
Screw Diameter |
Φ105mm |
L/DÂ Â Â Â Â Â Â Â Â Â Â Â Â |
30:1 |
Screw Material: |
38CrMoAlA adopt Nitrogenous treatment |
Heating zones: |
6 zones |
Butane Pump: |
1 set |
Digital Pressure Gauge: |
1 pc |
Fully-automatic Hydraulic filter changer: |
1 set |
Electrical Cabinet: |
1 set |
Motor: |
3 sets (4-pole, 55kw,by frequency exchanger) (4-pole, 2.2 kw, by frequency exchanger ) (4-pole, 5.5kw) |
D NO.2 extruder |
 |
Screw Diameter. |
Φ120mm |
L/DÂ |
32:1 |
Material |
38CrMoAlA adopt Nitrogenous treatment |
Heating zones |
6 zones |
Pressure gauge |
1pc |
Automatic water cooling system |
5sets |
Motor   |
4-pole 55kw by frequency exchanger |
E. Cooling System |
 |
Hollowness water circulation cooling |
1 set, as the dimensions by the customers |
F. Hauling-off System |
 |
Rubber Roller |
3 pcs, (according customer's requirment) |
Traction Speed |
3-31m/min |
Motor |
1x 4-pole, 3 kw (controlled by frequency changer) |
Counter  |
1pc |
Alarm system |
1set |
Haul-off type |
run in S route by self-friction |
G. Winding Device |
 |
Winding Pneumatic Shaft |
2 pcs (according customer's requirment) |
Torque motor |
2sets |
Turbine Reducer |
2sets |
Static Electricity Eliminator |
1set |
Alarm |
1set |
H. Die Material |
 |
Installation Power |
200kw |
Central height |
1000mm |
I. Weight |
8 T |
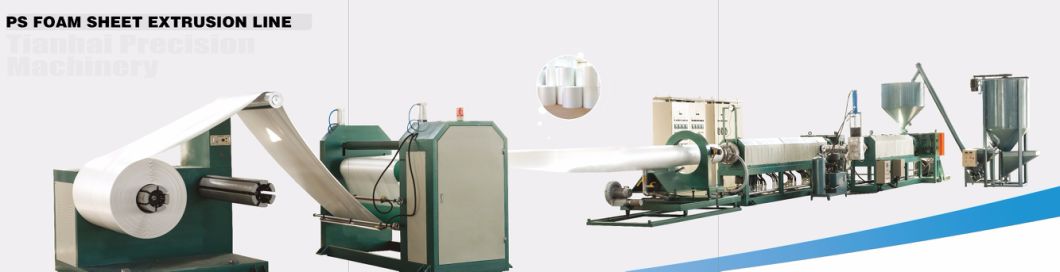
Â
2) GX-1100x1250 Fully-automatic  Forming Machine (with Crusher in line)
A.Technical data:
Â
A.Technical data:
Â
1.Control system |
 |
Automatic Control Cabinet |
1 set |
automatic Temperature Control Cabinet |
1 set |
PLC controller |
Adopt Emerson USA |
Touch screen |
Adopt Taiwan Weinview |
 |
 |
2.Automatic Pneumatic Feeding device |
1 set |
 |
Feeding length can be adjusted. |
 |
 |
3.Heating System, |
2sets |
Subsidiary Heating Zone /2 sets |
Adopt the far infrared radiation tile. |
 |
 |
4. Forming System |
Adopt hydraulic cyclinder drive |
Motor |
2 sets 7 kw |
Hydraulic stations |
2 sets |
Vacuum forming press |
60T. |
Forming area |
1040mm×1250mm |
Vacuum forming speed |
3-4s/mould. |
 |
 |
5.Cutting off System |
Adopt hydraulic drive |
Motors |
1 set 7.5kw |
Hydraulic station |
1 set |
Max. Punching |
100T |
Cutting off area |
1040mmx1250mm |
Cutting off speed |
3-4 s/mould |
 |
 |
6.Stacking System |
 |
Robot manipulator |
Servo motor control, Japan Omron Brand |
Automatically stack |
Adjustable,as customers' need |
Automatic counting system |
Adjusted, according to the customers' need |
Automatically conveyor |
Double Conveyor on two sides. |
 |
Controlled by Frequency Exchanger, Emerson USA Brand |
 |
 |
7.Scrap rolling system |
Automatically Crusher system on line |
 |
Automatically recycling system on line with pipes. |
 |
 |
8.Installation Power: |
180kw |
9.Power Supply |
3 phase 4 line 380V 50Hz |
10.Weight: |
14 T |
11. Crusher in line |
 |
Installation Power: |
11 KW |
Fully automatic conveying |
1 set |
Size: |
2mx2mx1.6m |
Weight:Â |
0.7T Â |
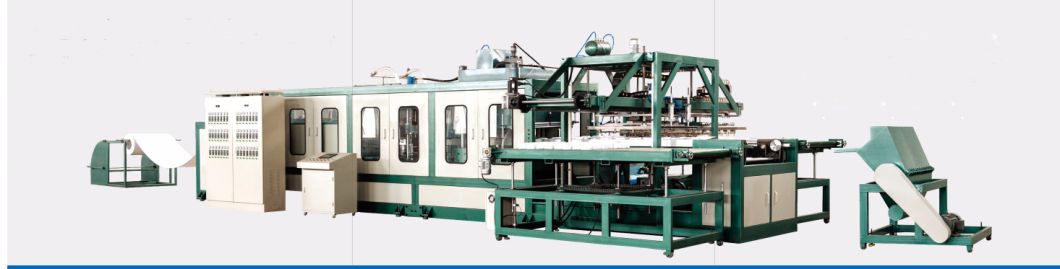
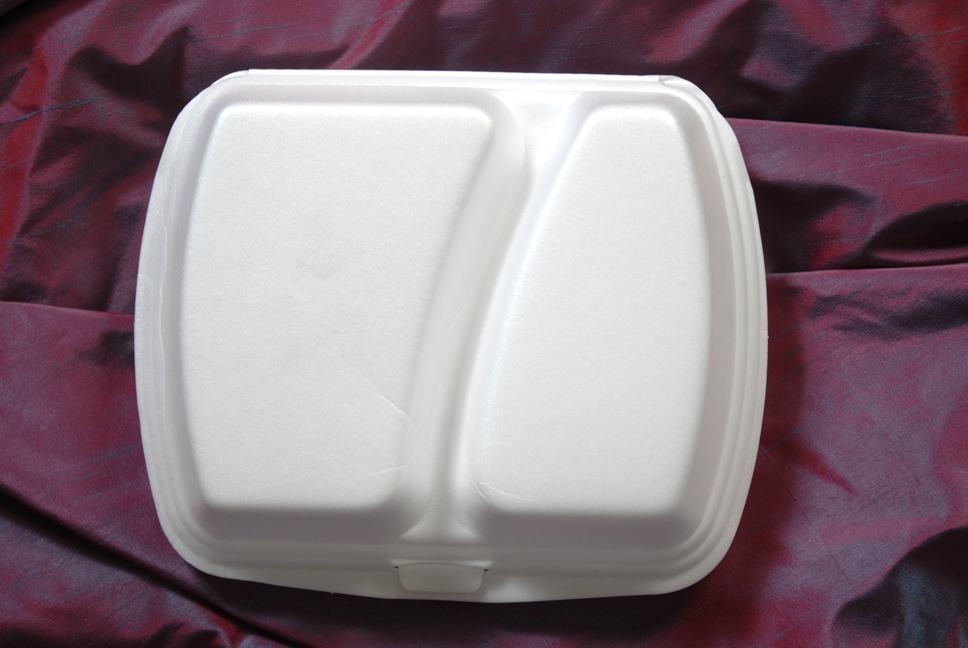
AA. Why choose us?
1) Technicians in here with more than 15 years experiences in the Plastic machines fields.
2) Happy Quality of machine , with turnkey projects from A to Z in option.
3) Happy PRICE.
4) Freight cost down with nice logistics solution.
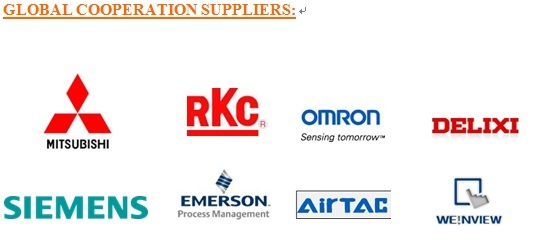
BB. what is our advantage ?
1) Â
the frame structure of our machines is magnificent strong and adopts superior materials to ensure the stability of equipment operation, even lasting for more than 10 years.
2)
the performance of extruder, thermoforming machine, recycling machine, etc, is much good, such as the working speed is much fast, and the capacity of our machine is much bigger.
3)
Supreme configuration.
There are imported electronic components and Chinese made brand device together, in order to assure the reliability of the equipment operation. Such as: PLC adopts the Japanese Mitsubishi, servo motor adopts the Japanese Omron, temperature control adopts Japan RKC, and frequency exchanger adopts German Siemens, and so on.
4) Â
the operation of the equipment is more humanizing, handle easily and simple to operate.
As the professional Plastic machine manufacturer, we keep pace with time, and keep the technical research.
5)Â
In addition, the equipment is improving technology continuously, paying more attention to the details of the performance improvement.
What we do is just to enhance the manipulative performance and to simplify daily maintenance.
6)Â
There is one point need listed, after-sales service of the equipment is generally more important.
We adhere to the principle of sincerity to customer service, considering the particularity of the equipment and daily maintenance.
7)Â Over sea office and quick back on line.
If there are some unexpected happens, we shall reply within 24 hrs and offer the solution projects, in order to ensure the interests of clients and the honor of my company.
8)Â
what's more , matching with complete spare parts service , for more than a year of the quality assurance period, the details as guarantee, we believe that the customer can trust our equipment and trust our team.
Not only sending machine out, but mostly for the machine running in the good condition.
Not only selling the machine to customers, but mostly let customers to make their more profits.
Good solution and service in here.
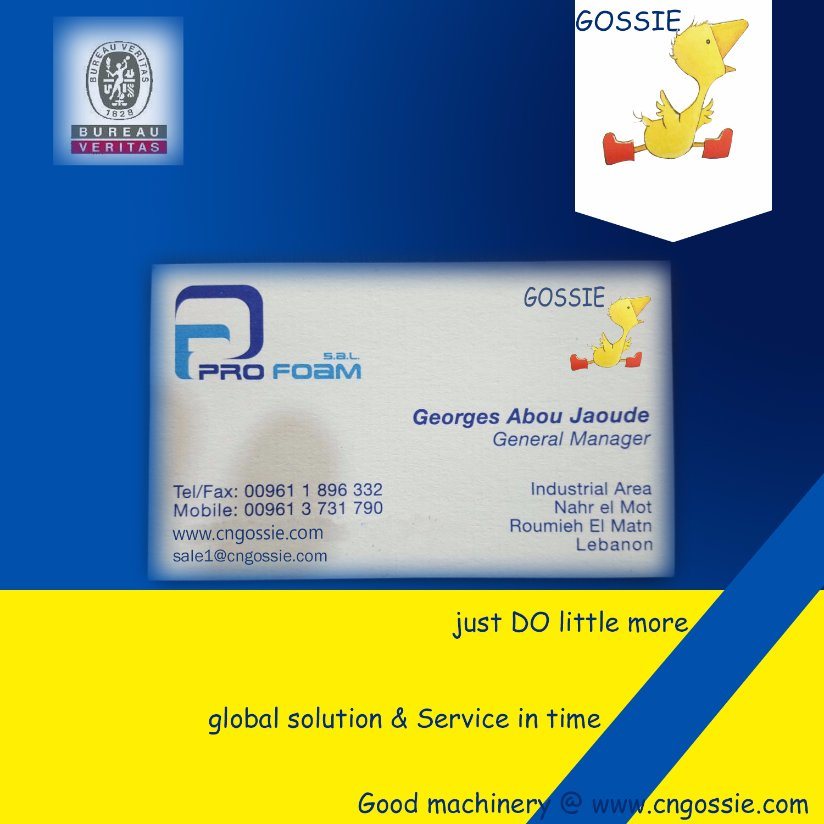
Â
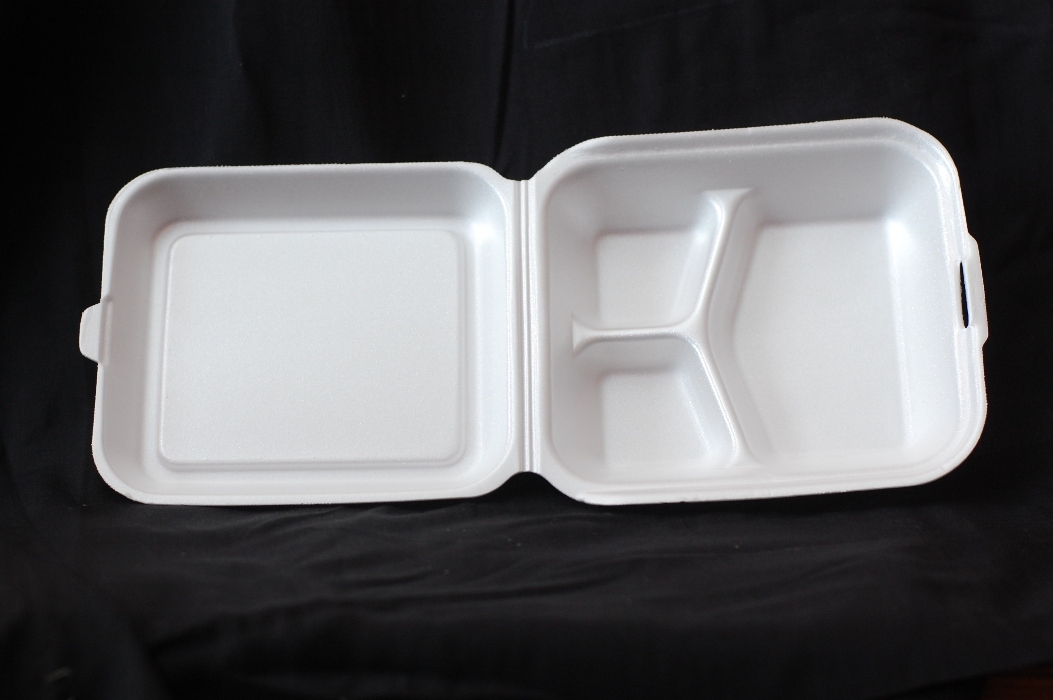
PS foam food box making machine, use the PS foam sheet made by the PS foam sheet extruder, as the materials.
throught changing the different molds to get the various kinds of colorful products, like the PS foam food box, PS foam food tray, egg tray, bowl, cake case, fruit tray, and absorbent tray to contain the meat, or fish or shrimp,etc,.
which is used for package industry.
Â
GENERAL INFORMATION:
Â
Â
Â
Raw material:Â |
PS granule, talc, butane and so on.   |
Finished products:Â |
Ps foam fast food box, foam tray, pizza box, hamburger, egg tray, and so on. (Depending on changing mold)Â Â Â Â |
Sheet thickness: |
1-5mm |
Sheet width:Â |
600-1200mm |
Capacity:Â Â |
180-240kgs/h |
Operator: |
6-8 workers |
Water consumpation:Â |
200kgs/24hrs |
Cooling water tower:Â |
20 T/ h |
Butangas consumption:Â |
45-50 kgs/one ton materials (based on the foam ratio range from 16-20) |
Air compressor : |
1.5 m3/min |
Installation power: |
550Kw |
Power supply : |
3 phase 4 line 380V 50Hz |
Work shop area:Â |
PS Foam Sheet Extrusion Line workshop: 25x8x4m (L*W*H) Fully-automatic Vacuum Forming Machine workshop :20x8x4m  |
Warehouse: |
Per raw material warehouse area 60M2 (at least) Per finished products warehouse area 60M2 (at least) Â |
Container |
3x 40'HQ containers |
Each factory has its respective advantage about what they done , and each manufacturer is good factory, which is the truth, and we believe it.
While here is us , Yantai gossie be your nice choice.
Â
Main equipment and technical parameter
1). GX- 105/120 PS Foam Sheet Extrusion Line
1). GX- 105/120 PS Foam Sheet Extrusion Line
Components: |
 |
A.Mixer |
 |
3D Printing Auto Production Line 3D Printing Auto Production Line,3D Printed Solid Sand Mold,Resin Sand Molds For Casting,Small Build Volume 3D Printer Guangdong Fenghua Zhuoli Technology Co., Ltd , https://www.fhzl3d-print.com |