SGL Lewei Jeans Co., Ltd. is a joint venture between Yixing Lehe Textile Group and SWIFT, a well-known American denim company, which produces high-grade denim. It is a leading supplier of raw materials to many major brands in the world. The main products are adult men and women. , Juvenile taking denim, uniforms, sportswear, casual denim, special dark blue denim, primer, jacket, coated denim, Tencel, elastic and other special fiber denim.
Dr. Bai Jingquan made a report at the conference Lexiu Textile Group is the “Top 10 Enterprise†in the national printing and dyeing industry. The production line is equipped with the world’s newest MorrisonRopeDye dyeing machine, WestPoint Ball Machine, fully automated Zux Sizing Machine, and Picanol Omini Plus 800 and GAMMAX woven fabrics. Machine, singeing - mercerizing - sloping - stereotyped finishing integrated Monfort and Monfort EX pre-shrinking machines. The production plant has more than 50,000 square meters of individual factory buildings, and the total area of ​​the park is 500 mu of land. By the end of 2007, it has already launched more than 100 denim varieties in Europe, America and Japan. The company adopts the American enterprise management model and management process. Each branch and workshop fully manages the process and on-site control through the automation system and ERP system, and the central integrated control.
I. The Development Bottleneck of the Textile Industry The textile industry is a labor-intensive traditional industry with long production processes, many control conditions, and poor process reproducibility. And it is an order-based, low-value-added processing model. It is mainly based on passive marketing and has low competitiveness. How to realize printing and dyeing automation within the industry is the key to improving the industry level.
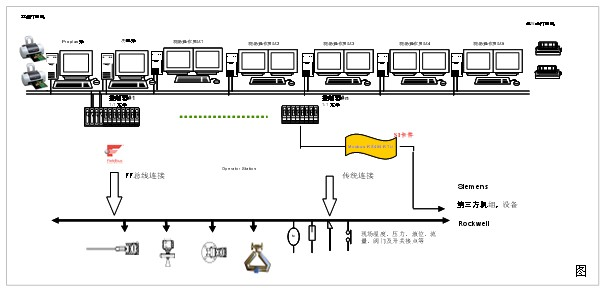
After analyzing the current problems, our company realized that information technology and FOUNDATION fieldbus technology will bring new opportunities for development in the textile industry. Faced with the current intelligent level of textile machinery equipment, it is possible to make centralized control of process conditions possible.
Figure 1: Schematic diagram of system configuration of Levi denim production line After the process changes in the long-distance pipeline have been effectively controlled, the predictive maintenance of equipment has changed the concept of traditional equipment maintenance. Accurate measurement of data such as flow, pressure, and temperature of the equipment provides a necessary basis for detailed control of process costs.
In the process of the transformation of the textile industry from traditional industries to modern ones, fieldbus-based control technologies provide opportunities for the decentralized, networked, and intelligent development of textile industry control systems. It provides necessary conditions for knowledge-based and product-based companies.
Second, Levi denim production line introduced the use of FF fieldbus technology to control the operation of the core machine production line. Including: 24 Morrison Dyeing Machines, Double Slots Double Zircon Sizing Machines, Monforts Stabilizers, Monfort Shrinking Machines.
The main control system of the device selects DeltaV. There are 11 host computers, including 1 ProPlus station, 1 engineer station, 7 operator stations, and 2 application stations. There are 512 pairs of MDPlus controllers and I/O meter interfaces on site. In order to improve the overall level of control, the system has installed advanced intelligent equipment management software AMS. (See Figure 1)
The connection and configuration of FF field instruments use P+F Powerhub and bus power conditioners and P+F basic physical layer diagnostic modules, a total of 78 network segments, an average of 6 devices on a network segment, the most There are 10, the least 4. Of the more than 120 control loops, the majority are single-loop, and the PID function that performs the control function is decentralized to the smart valve positioner (see Figure 1).
Third, the textile industry to consider the choice of FF technology The textile industry production line is long, the traditional control program is not conducive to centralized management and decentralized control. The bus application can bring the following advantages to the factory:
l centralized management: all information can be entered from the bottom-up control system screen display, alarm, remove the factory blind spots.
l Decentralized control: PID control is dispersed to the site, reducing risks, avoiding parking, saving costs, and improving system reliability.
l Reduce investment: Save cables, bridges, reduce the number of cabinets and space, improve debugging efficiency, and speed up project implementation.
l The field device has an intelligent early warning function and can perform pre-diagnosis and maintenance. Improve equipment maintenance methods to avoid accidents and save factory routine maintenance costs.
Fourth, FF practical application advantages - installation cost savings 1) compared with the traditional PLC program, analog signal cables reduced by 75%, I / O card and the bottom plate is also reduced accordingly; the number of cabinets than the traditional program to save half. (See Table 1)
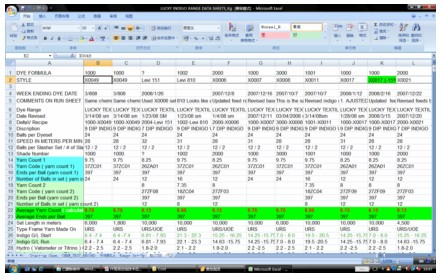
Figure 2: The FF system control network shows clear process routes and is easy to operate
3) The use of AMS equipment management software to realize remote debugging, configuration and fault diagnosis of the instrument allows the instrument personnel to know the situation of the field instrument in the control room.
Fifth, FF bus application experience 1) to fully understand the importance of technical training:
Compared with traditional equipment, FF bus control system has some differences in maintenance and use, and the methods and concepts of maintaining instruments are also different from traditional systems.
2) It is necessary to give full play to the functions of the FF intelligent system and equipment to facilitate loop testing, instrument calibration, equipment early warning, status analysis, and equipment management. The instrument management team also needs to receive technical training, accumulate experience in applications, and continuously improve applications. Level.
3) Must pay attention to the installation quality:
The FOUNDATION fieldbus is a two-way, all-digital communication system that can bring a wealth of on-site information to the factory. In order to ensure the high quality and stability of the communication, the quality of the construction during installation is critical.
According to our experience with the bus, over 80% of communication failures are caused by installation problems. Checking the network segment according to the bus installation standard after the completion of the first construction and during the subsequent maintenance is an important means of eliminating communication faults.
Six, FF bus application of attention in the textile industry, FF bus control system overall installation is better, but there are some problems that need attention:
Some field instrumentation signal lines are reversed. According to the FF specification, field instruments are insensitive to the positive and negative signals and do not affect signal transmission. However, attention should be paid to this issue during installation and construction.
The dust on the production line is relatively large. Because the controller cabinets are placed on the site, the controller, FF interface cards, and FF power supply regulators are extremely susceptible to dust accumulation. Therefore, the dustproof work of the cabinet needs attention.
FF bus application experience - Condensate problem In Levi denim production line, due to process reasons, there is a large amount of water vapor generated. Condensate enters the meter through the cable entry, causing instrumentation failure on the network segment. In this regard, waterproofing should be done during construction, or holes must be drilled into the cable to allow condensate to drain out of the hole.
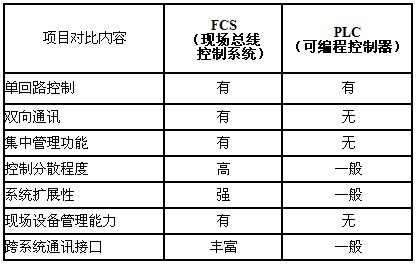
Table 1: Compared with PLC, FF field bus has very good information transmission characteristics
The FF fieldbus control system applied to our company's denim production line has been put into operation since December 2007 and it is in good condition. The control system uses Emerson's DeltaV. The configuration is simple, easy to learn and use, and it replaces the traditional PLC control on the production line. DeltaV system software Inspect can effectively monitor the health status of the control loop and field instruments, and the operation of the plant is clear at a glance. (See Figure 2)
Through practice, we have realized that the field bus control system has revolutionized the traditional control system structure, and has made the automatic control system move toward the direction of intelligence, digitization, information, networking, and decentralization.
At present, FF bus has not reached large-scale application in the textile industry. As the fieldbus control system can replace the traditional production line PLC control, but also has a very good price. With the popularization of on-site industrial bus products, on-site industrial bus system technology will surely be widely used and developed in textile automation.
The application of FF provides a possibility for textile enterprises to provide knowledge-based companies, but automation systems are not everything. Its application effects ultimately depend on the people and the enterprise environment in which it is applied: the top-down understanding of enterprises; the strategy and methods of enterprise research and development Transformation; the matching and training of professionals; the supporting information systems, etc., all of these conditions must be combined to achieve a multiplier effect.
Cooling capacity 20kW-50kW
Characteristics:
1. Structure: Panels and base frame are made from galvanized steel protected with polyester powder painting to ensure total resistance to atmospheric agents.
2. Compressor: Hermetic scroll type compressor, equipped with the crankcase heater and thermal protection with thermal overload cut-out and crankcase heater mounted on rubber vibration isolators.
3. Axial fan: External rotor type axial fans, equipped with single phase direct drive motors, low noise 6 poles, protection level IP54, provided with a protective outlet grille.
4. Evaporator: High efficiency and low pressure drop stainless steel (AISI 316) water exchangers, with anti-freeze heating element (option) and differential pressure switch, factory insulated with flexible close cell material
5. Condenser Coils are consisting of seamless copper tubes mechanically expanded into blue hydrophilic aluminum fins, 100% fully quality tested; sub cooling circuit to prevent freezing at the base (optional); protected with metal grill.
6. Desuperheater: High efficiency stainless steel brazed plate heat exchanger, factory insulated with flexible close cell material(optional).
7. Refrigerant circuit: Copper tube connection with charge valve, filter, sight glass, gas-liquid separator, thermostatic expansion valve, low pressure switch with automatic reset, high pressure switch with manual reset. The heat pump unit is completed also with 4-way valve, liquid receiver and one way valve.
8. Water circuit: Built with air vent valve, water drain connection, and female-threaded hydraulic connectors. Water pump (8kW-30kW), differential pressure switch. Expansion tank (8kW-30kW)
9. Electric panel: Compressor contactor, Compressor protection breaker, Fan motor protection breaker, Control circuit protection breaker, Phase sequence relay (only for 3-phase), Programmable microprocessor controller
10. Optional: Additional electric heater embedded in the coils for defrosting in low temperature ambient. It must be factory installed; Stainless steel covering; Remote condenser; Tube in tube heat exchanger; Water circuit electric heater.
Mini Chiller
Mini Chiller,Commercial Mini Chiller,Central Mini Chiller,Air Cooled Mini Chiller
Jinan Amrta Air Conditioning Co.,Ltd , http://www.amrtaac.com