Shenmu Company began to introduce RBM system and its supporting software from July 2005. In 2006, it officially started using RBM system to guide the development of the maintenance plan. The entire construction process can be divided into the following steps.
L.1 Equipment grading First, all equipments of a power plant are divided into various systems such as a steam turbine system, a boiler system, an electrical system, and a thermal control system according to different functions, and then each system is refined until the specific equipment. In general, each equipment The system contains 5, 6 levels, as shown in Figure 1, the grade of 11 condensation pumps.
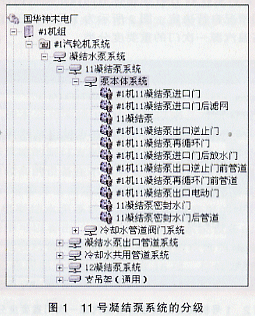
The classification of No. 11 condensate pump system can be seen from Figure 1.
The rating of other systems is similar to this. When grading equipment, attention should be paid to putting equipment that serves the same function together. For example, the pumping oil system and the turbine oil system belong to different functional modules and cannot be put together.
Through the equipment system, it is possible to search for equipment in a targeted and fast manner, and to know the name, model, manufacturer, production date, KKS code, position in the power plant, and detailed technical specifications of the equipment. The purpose of establishing the equipment system is to prepare for the classification and evaluation of the equipment in the next step.
1.2 Classification of importance degree After the establishment of the equipment system, the importance of the equipment in each system is classified, and all equipments are classified into high importance equipment or low importance equipment. When classifying, consider the safety of the equipment, the quality of power generation, and the economic efficiency. That is, how large is the impact on the person and the environment after the equipment failure, how much the impact on the power grid is, and how much the cost of the equipment needs to be repaired and the duration of the equipment How long, etc., after a comprehensive consideration of these factors, to calculate a value, this value is compared with the standard value, the device above the standard value is a high importance device, the device below the standard value is a low importance device. It should be noted that the degree of importance of the equipment is related to the location of the power plant and local policies. The same equipment is a highly important equipment in the A plant but may be a low importance equipment in the B plant.
The calculation method used for importance classification is the S, Q, C, and D methods. First, the functional failure of the equipment is assumed. This assumes the influence of the fault on the power generation system (degree of harm), S (impact on safety), and Q. (Effects of power generation quality), C (equipment repair costs), and D (equipment repair period), etc., are evaluated, and the degree of damage when each device fails is determined based on the evaluation result, and the importance of the equipment is determined based on the degree of damage. degree.
The assumption of failure of the equipment is the premise of classification of importance. The assumption of correctness relates to the correctness of equipment classification and the accuracy of the next work. It is assumed that natural disasters and human error operations should not be taken into account when failures, and multiple multiples are not assumed. Failure, otherwise it will make the classification inaccurate. As for the setting of the values ​​of S, Q, C, and D, it is determined on the basis of the conditions of each plant. Figure 2 shows the importance classification of the high-temperature steam source primary door of the front shaft seal of No. 1 engine high pressure cylinder.
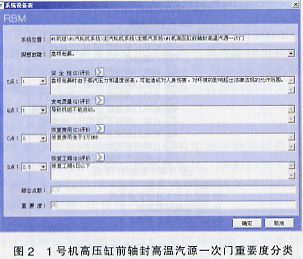
1.3 Risk Assessment on High-Importance Equipment Risk assessment is performed on high-priority equipment to determine the level of risk of the equipment or components. The risk assessment is divided into two aspects: first, the degree of fault proneness; and second, the degree of damage. Failure proneness mainly considers the occurrence rate of defects or accidents and the implementation of preventive measures during the maintenance period of the equipment or components, the accident rate of the same type of equipment or components, the implementation of preventive measures, and the aging of equipment or components. Trends and other factors. Through the calculation of these four factors, the failure-prone value of the equipment or components can be obtained - 1, 2, 3, 4, and 5 levels, with the lowest level 1 and the highest level 5, and the degree of damage is mainly considered after the failure. , environment, and the impact of the grid, as well as repair costs, duration, and other factors after a failure. To calculate the hazard value, first imagine a fault. This fault must be the most frequently occurring and the largest fault. For a general device, multiple faults cannot be assumed, and then based on the above factors, the above factors are finally calculated. Degree of damage. The hazard values ​​are grades a, b, c, d4. Class a is the highest and class d is the lowest. The hazard level value is the horizontal axis, and the failure probability value is the vertical axis, which forms the risk matrix diagram. The risk values ​​of the equipment or components can be found on the risk matrix diagram. The risk values ​​are A, B, C, D4, Grade A. The risk is the highest and the D-level risk is the lowest, as shown in Figure 3.
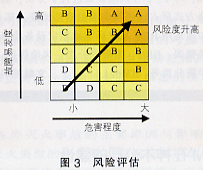
1.4 Determine maintenance standards The maintenance standards include the contents of inspections, maintenance methods, and maintenance intervals. When the maintenance standards are established, they should be based on the old inspection standards, and comprehensively consider the maintenance records and the weaknesses of the equipment. There are differences in the method of formulating maintenance standards for high and low importance equipment.
1.4.1 Establishment of low importance equipment maintenance standards When determining the maintenance standards for equipment of low importance, comprehensive consideration shall be given to the impact on the thermal efficiency at the time of failure, the level of recovery costs, and whether there are abnormal operations or not. These three aspects are collectively referred to as the degree of influence. Through the comprehensive evaluation of these three factors, the impact of low-priority equipment is divided into three levels: large, medium, and small.
According to the classification result of the degree of influence, and considering whether each device can implement condition monitoring, the optimal inspection and repair method is selected.
(1) Equipment that can perform condition monitoring can, in principle, be selected for conditional overhaul. However, if it is a highly influential device and the frequency of failures is high, consider choosing a periodical overhaul. When a periodic inspection is selected, the maintenance cycle uses the best inspection cycle of the factory or other reference manufacturer, that is, the equipment with the same functions, weak points, and aging parameters, and the longest inspection cycle obtained on the premise of a fault.
(2) Equipment that cannot perform condition monitoring should, in principle, have medium and large equipments that are selected for periodic maintenance, and equipment with low impact should be selected for overhaul.
1.4.2 The development of high importance equipment maintenance standards The maintenance standards for high importance equipment should be based on the risk level determined by risk assessment. At the same time, refer to equipment specifications, periodic maintenance records, technical documents, and the actual operation of the equipment to be evaluated. , future operating plans, manufacturer's technical specifications, operating data and other information, fully grasp the characteristics of the equipment, determine the equipment maintenance standards.
The degree of risk is high for equipment with a degree of risk. Regular inspections should be used, and the original inspection cycle cannot be extended. At the same time, we will conduct technical discussions on equipment countermeasures such as replacement of main components and formulate plans to reduce risk.
The risk is Class B equipment with high risk. In principle, it is not possible to reduce the maintenance content and extend the maintenance period. However, after obtaining the approval of the professional technical conference, it is possible to reduce the maintenance content and extend the inspection period.
The degree of risk is Class C equipment, with a degree of risk. Under the premise of obtaining professional technical meetings, it is possible to reduce the contents of inspections and extend the maintenance cycle.
The risk is Class D equipment with low risk. Under the premise that the professional and technical conferences obtain consensus, it is necessary to actively study the reduction of maintenance contents and extend the inspection period.
It should be emphasized that regardless of high or low importance equipment, inspection standards are not static and the situation has changed. For example, when new maintenance data are acquired after the implementation of a periodic inspection, technical changes, equipment changes, etc. To re-evaluate the risk, for the re-evaluation of the risk, the revision of the inspection and repair standards, the results of each repair standard revision must be determined through professional and technical personnel discussions.
Second, the specific requirements for the use of RBM In order to maximize the role of RBM systems, Shenmu company made detailed provisions for the use of RBM systems: (1) Each time before the scheduled maintenance overhaul project, the head of equipment maintenance department should A meeting attended by professionals at all levels was held, and discussions were carried out based on RBM's overhaul schedule to determine the items planned for maintenance. For areas that do not meet the RBM maintenance plan, details should be provided in the minutes of the professional meeting. (2) Within 30 days after the completion of Class A inspections, and within 5 days of Class B and C overhauls, within 7 days of Class D overhaul or accident repairs, the RBM will be entered by a professional supervisor of the Equipment Maintenance Department, based on the new overhaul. Resume revised maintenance standards. (3) In December of each year, a professional meeting of the equipment maintenance department should be held. Professional professionals at all levels will review the importance, risk, and maintenance standards of RBM equipment and make necessary revisions.
Third, the superiority of RMB Shenmu Company has introduced RBM for six months and has built a good platform for the development of maintenance strategies for Shenmu Company. Not only can improve the efficiency of maintenance and repair personnel, but also improve the accuracy of planned maintenance projects, so that the overall reliability of the unit has been improved, and maintenance and repair costs reduced. Specifically, there are the following advantages: (1) Improve the reliability of the equipment. Since the implementation of the spot inspection and repair system, all planned maintenance items and inspection and repair periods are determined by the experience of spot inspection personnel. Whether the accuracy is related to the level and experience of the inspection personnel has a lot to do with, and lack of effective assessment methods. Because of the unplanned downtime caused by inaccurate maintenance projects, RBM can systematically evaluate equipment overhaul periods and projects. The final maintenance standards are formulated after comprehensive consideration of various conditions, and all members of the expert group are integrated. The comments have improved the accuracy of maintenance projects and also improved the reliability of the equipment. (2) Reduced maintenance costs. The equipment that was originally considered to be very important, such as a feed pump, was to be overhauled each time the machine was shut down. The cost of overhaul and maintenance was high and there was a phenomenon of overhaul. Through RBM's assessment, it is considered to be a low-priority equipment (because there is a reserve), so that its inspection period is prolonged and maintenance items are reduced, thereby reducing maintenance costs. (3) Easy to use. RBM provides excellent software to manage equipment accounting, inspection history, equipment classification, risk assessment and maintenance standards. The interface design is reasonable, data editing and viewing are convenient and quick, easy to learn. And provide KKS coding interface, providing the conditions for future data sharing and BFS + +.
IV. Comparison of the effect of Shenmu Company before and after implementing RBM Shenmu Company has implemented RBM for half a year and has reconsidered and established the overhaul cycle and overhaul methods for all equipment. It has achieved significant results in the formulation of maintenance strategies, and some of the maintenance costs are high. The equipment has extended the overhaul period without affecting safety, and the overhaul method has changed from regular overhaul to overhaul. Figure 4 is a statistical table of changes to the maintenance strategy of Unit 1 condensate pump system equipment. It can be seen from the table that there are 9 items of maintenance items for the system equipment after the RBM review, and there are 0 items for shortening the inspection period. There were 16 changes at the end of the inspection cycle. There are six items of overhaul methods from regular maintenance to conditional overhaul, and one item of conditional overhaul to regular overhaul.
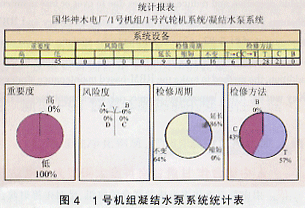
For specific equipment, No. 11 condensation pump outlet electric door, after the RBM analysis, the inspection period was extended from the original 36 months to 60 months; No. 11 after the inlet of the coagulation pump inlet filter repair method from 24 months Regular inspections become status inspections. Figure 5 shows the results of the analysis of the 11 condensate pump electric outlet gate.
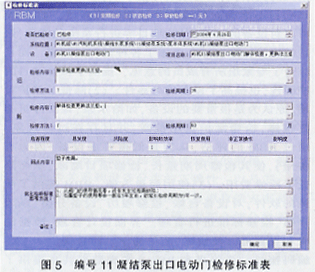
V. Conclusion The extensive application of RBM in various industries, especially the application of all thermal power plants under the Kansai Electric Power Co., Ltd. in Japan, illustrates the advanced nature and effectiveness of RBM systems. However, even the best systems and methods are simply introduced and have no effect, and they must change the traditional sense of concept. Therefore, a thorough understanding of the RBM ideology, a mastery of its methods, and the implementation of the corresponding management system should be used in conjunction with the actual situation. A good RBM system is the only way to make the RBM system play a full role.
Structures of Wood Shredder:
1. Connector
This is the connector for be trailed. Sure, it can be made according to the requirement of customers.
2. Hydraulic oil tank
The oil tank is 38L.It guarantees that you can use it longer than ordinary one.
3. Blades
There are two steel dual edge fly wheel blades on the WC-40. Sure, if you need four blades on it, we can produce for you. The blade is made by tool steel.
4. Bed plate
There is one bed plate on the inner of the feeding chute. It can guarantee the service life of chipper.
5. Discharge chute
The discharge chute gives excellent airflow and easy adjustablility.
6. Tyres
The diameter of the tyre is 53cm. It is always used on minibus in China. Another choice is turf tyres.
Details of Wood Chipper
Details of diesel engine wood shredder
---Mobile with wheels, diesel engine, specially designed for out door working
---Hydraulic reversing valve control feeding, Feed inlet volume:20*22cm
---Diesel power: Weichai brand ,Less consumption and electric starter.
Diesel Engine Wood Chipper,Towable Diesel Engine Wood Chipper,High Output Diesel Engine Wood Chipper,Mobile Diesel Engine Wood Chipper
Shandong Rotex Machinery Co.,Ltd , http://www.woodpelletmachinery.com