Mold Description | Â |
Mold Standard | DME or HASCO |
Mold Base | LKM,DME,HASCO,FUTABA |
Cavity /Core steel | H13,S-7,S136,SS420,NAK80,P20 and other material as requirement |
Hot Runner | Yudo |
Cavity | Multi or single cavity |
Gate type | Side gate,Sub gate,Pin point gate,Edge gate etc |
Hydraulic cylinder | PARKER, TAIYO, STAUBU, JUFAN |
Mold components | DME, Progressive, PCS, Punch, Royal, etc |
Steel Treatment | Heat Treatment, Nitriding, Chrome Plating |
Surface finish | SPI standard, VDI EDM, Texture, etc |
Texture | Mold-tech, Yick Sang, Ni Hong ,Tanazawa etc |
Plastic Material | PP, PC, ABS, PE, HDPE, PET, POM, PMMA, PA(GF), PBT(GF), PVC, PPS,etc |
Product weight | 5.0g~15kgs |
Mould Life | 0.3 Million Shots- 1Million shots |
Delivery Time | 4Weeks T1 samples , exact time depends on Mould Complexity |
Packaging | Free-Fumigation Three-Plywood case for moulds, cartons for parts |
Design software | CAD,UG, Pro E, Solidworks |
Value-added service | Dust-free Spraying, Silk-screen Printing, Ultrasonic Welding, Thermal Bonding, Assembling, Prototype |
Service area | Transparent, Over mold, double color, air assistant forming, deep barrel, Design R&D, Assembly |
Our Capability | Auto, Aerospace, Household, Electrical, Industrial, Medial, Toys, Office, Cosmetic, Outdoor, OA Equipment etc |
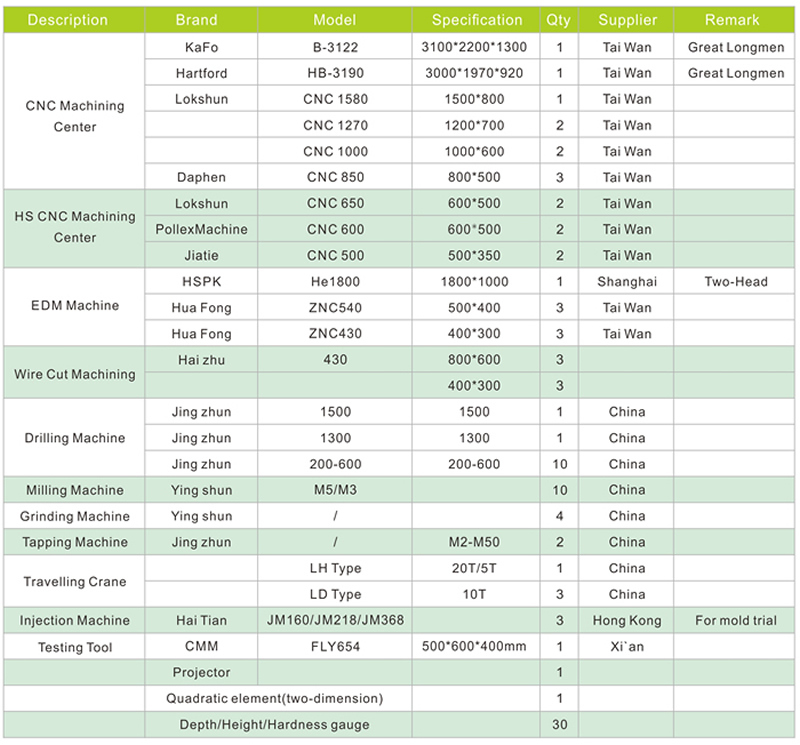
Sample Show
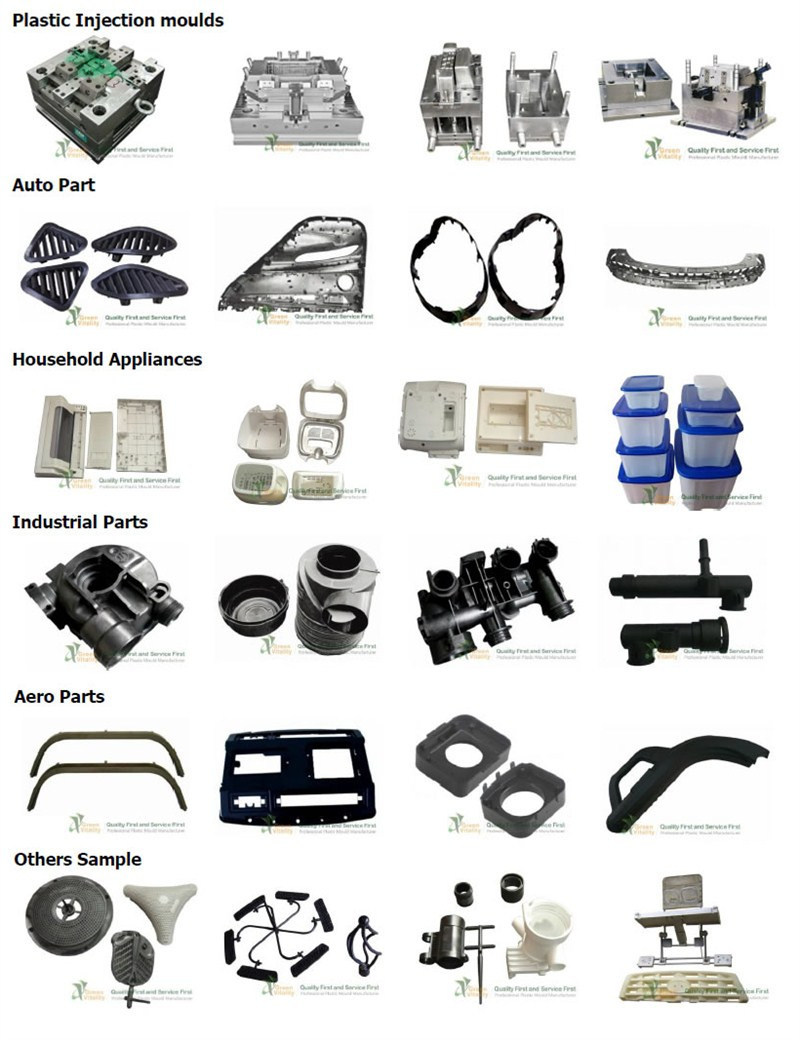
Production process
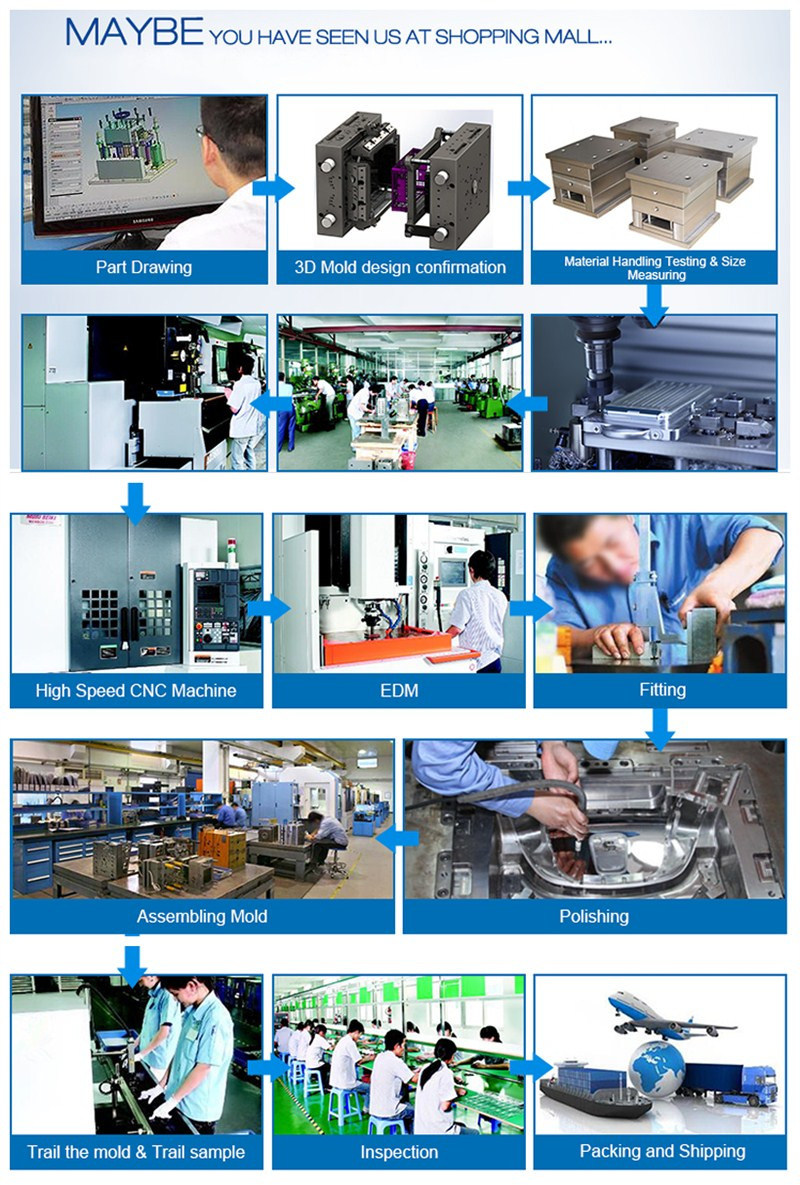
About us
Green Vitality was founded in 1993,as starting from CNC processing in a small tooling building in Chang'an town, with more than 20 years experience in custom tooling and injection molding, nowadays we have become one of the global famous mold makers in manufacturing large plastic injection molds. With the modern business management system and ISO9001:2008 Quality System guideline, the sophisticated production techniques, the advanced manufacturing equipment, and our qualified and dedicated team, we are full of capabilities and have great confidence in offering you professional one-stop solution of mold designing, mold making, injection molding and beyond-value service. We serve a broad range of customers in the field of Auto Parts, Aero parts, Household Appliance, Industrial and Beauty. Green Vitality make over 400 molds per year, mainly of the molds and plastic parts are exported to America, Germany, France, Turkey, Italy and other countries worldwide. We have established long-term cooperation with our clients and are continually improve top quality molds and plastic parts to our clients, establishing close strategic partnership to keep customer's satisfaction and success, growing up together with customers.
Factory Profile
6000 square meters mold making workshop, 8,000 square meters injection workshop.
With 160 employees, including 20 engineers, mold maker 65 people, injection molding 60 people.
Factory Capability:
40 molds per month (Max.)
Max. mold size 3200x2200mm, Max. mold weight 25 tons
Service Scope:
Expert in Auto Parts, Aero parts and Household Appliance large plastic molds
Plastic parts injection
Prototype parts
Market Advantage:
Top quality mold and plastic parts
Reliable service
Contact us
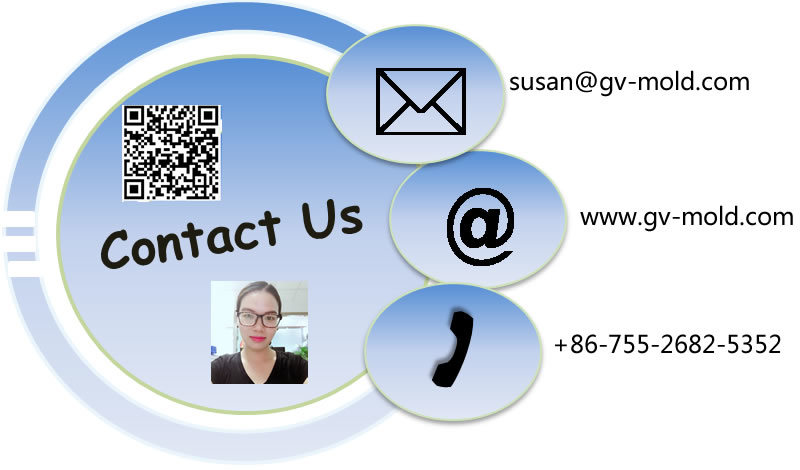
Â
Ball Joint:
The main function of the Ball Joint is to realize the upper and lower bounce and turn motion of the wheel.
Structure:
There are two kinds of main structure of the ball joint: one is spherical joint combined with the whole joint, the other is a hemispherical joint combined. Before using helical spring structure preloading and wear compensation, now what is widely used is elastic and lubrication synthetic resin tee which can reduce the cost and improve the maneuverability and stability. In addition, the material and shape of the dust cover, oil type has greatly improved, cancel the grease nozzle,of free maintenance.
Ball joint is mainly composed of an end cover, ball pin, tee and dust cover form.
Connection mode:
Due to the size and type of the spatial arrangement of the Control Arm, ball joint is connected with the control arm is as follows, bolt or rivet connection, directly pressed into the control arm and the control arm as one. From the ball head pin development trend, now more and more with the control arm as a whole the fixed ball pin, to meet the needs of small space occupation, convenient loading and low cost requirements. But the type of ball head pin of the service life of the demand is higher, so as to avoid the abrasion of the ball head pin or a failure. The whole control arm and the steering knuckle ball pin connection adopt 1/6~1/10 taper fitting manner.
Perforce Requirement:
It should have sufficient swing angle, in order to meet the requirements of wheel jumping up and down; small friction moment is to ensure that the steering important factors and easy manipulation; should not be caused by clearance of wheel shimmy and abnormal noise; good sealing performance, to ensure that the ball head pin can be used in water and low temperature environment should have the strength and durability; enough to withstand the force and vibration, the wheel came.
Manufacturing:
For independent suspension front and rear suspension of the ball head pin is an important safety component protection, must be used to ensure the quality of the production process.
1)Attention to the full joint. For hot forging, cold forging, pressing or casting method for manufacturing blank, then cutting. Control of materials and heat treatment is a key factor.
(2) Ball pin machining way for cold forging products is the mainstream. In the heat treatment of the material control is the key factor, in addition to the products of conical connection type, its size accuracy is the key factor of stable fatigue limit, need to take measures in size control of cold forging;
(3) Polyacrylate and polyester elastomer synthetic resin material structure with elastic effect to become the mainstream. In this structure, need tee shape, material design measures, to ensure the production of stable precision molding in the mold, making the fine The degree of control is the key factor.
(4) The structure of ball joint assembly, assembly methods are different, but most of the rolling wheel is the main way. As to prevent the process of different products, bad products, assembly error and so on, take corresponding measures to prevent mistakes, also used to check the torque. Shake angle digital inspection machine, and combining them together to set in the procedure.
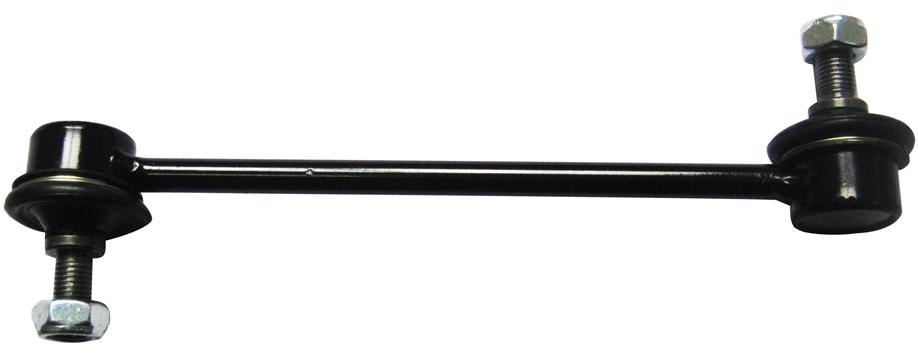
Ball Joint
Ball Joint,Rod End Joint,Rack End Joint,Auto Tie Rod End Ball Joint
VESTA Motoring Ltd , http://www.vesta-industry.com