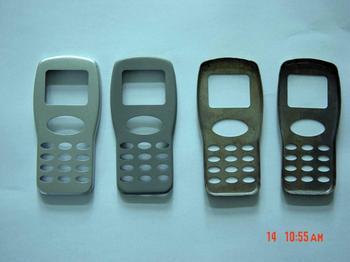
It is understood that magnesium is a very light metal element, and its alloy with other metals is light and rigid, and it is a very good modern industrial structural material. However, the disadvantage is that magnesium alloy stamping performance is poor and difficult to form.
Therefore, starting from 2010, the Chongqing Institute of Science and Technology and the National Engineering Research Center for Magnesium Alloy Materials of Chongqing University have jointly tackled the problem and proposed techniques such as one-way multi-pass bending, which lays the foundation for the preparation of magnesium alloy sheet and room-temperature stamping. A good technical foundation has also been developed for the stamping process of the notebook housing and car seat seat.
"Magnesium alloy stampings are light weight and high strength, and they are flatter and smoother in appearance. They are suitable for lightweight, portable electronic products." Luo Baihui, general secretary of the International Die and Metal & Plastic Industry Suppliers Association believes that the background of energy conservation and emission reduction Under the car weight loss has become a trend. The application prospects of magnesium alloys in the automotive industry will be very good. At present, Chongqing is making great efforts to promote the development of the notebook computer industry. This type of magnesium alloy stampings will have broad application prospects.
Magnesium alloys are about 1/3 lighter than aluminum alloys and about 3/4 lighter than steel, making them "reduced" for cars. In general, the car loses 100 kilograms of weight, and the fuel consumption will be reduced by 6-8%, thus achieving energy conservation and emission reduction. After testing, the stamping pass rate of the magnesium alloy laptop casing developed by the project team has reached 85%.
It is understood that during the implementation of the project, the project team conducted a test on an ordinary car. Compared with magnesium alloy steel plate used in the driver's seat, the weight reduction rate reached 65.6%.
It is reported that the project team has applied for 4 invention patents, established 2 pilot production lines, and is ready to further promote the application and industrialization of relevant results.
At present, the key to industrialization is to reduce the raw materials and stamping costs of magnesium alloys through technical means. Due to the current high cost, relevant results will be the first to be applied in high-end notebook computers and automotive products.
Desktop Dispensing Machine,Desktop Industrial Robot,Spray Adhesive Table Robot,Cnc Glue Dispensing Robot
CIXI TIANHAO ELECTRIC CO.LTD , https://www.nbtianhao-auto.com