I. Introduction
Laser cutting is a widely adopted technology in the manufacturing industry, known for its ability to produce precise and intricate cuts in a variety of materials. This technique uses a high-powered laser beam to melt, burn, or vaporize material, resulting in a clean and accurate cut.
Due to its efficiency and versatility, laser cutting has become an essential tool for manufacturers across various sectors, including automotive, aerospace, electronics, and more.
The objective of this article is to provide a detailed examination of the advantages and disadvantages of laser cutting. By understanding both the benefits and the limitations of this technology, manufacturers can make informed decisions about whether laser cutting is the right solution for their specific needs.
The article will cover the basic principles of how laser cutting works, discuss the different types of laser cutting technologies, and delve into the specific advantages and disadvantages associated with this method.
II. What is Laser Cutting?
Laser cutting is a precise and efficient method used to cut a variety of materials, including metals, plastics, wood, and more. The process involves directing a high-powered laser beam onto the material, which heats it to the point of melting, burning, or vaporizing. This concentrated energy allows for extremely accurate cuts with minimal waste.
The laser cutting process can be broken down into several key steps:
- Design and Programming: The cutting design is created using CAD software and then converted into a machine-readable format known as G-code. This code instructs the laser cutter on the exact path to follow.
- Material Preparation: The material to be cut is placed on the cutting bed. It may require specific preparation, such as cleaning or securing in place.
- Laser Cutting: The laser beam, generated by a laser resonator, is directed onto the material. The resonator can contain various elements, such as CO2, fiber, or Nd:YAG, depending on the type of laser cutter used.
- Focusing the Laser: The laser beam is focused onto a small spot using lenses and mirrors. This focused beam heats the material rapidly, causing it to melt, burn, or vaporize.
- Cutting Process: As the laser moves along the path dictated by the G-code, it cuts through the material. An assist gas, such as nitrogen or oxygen, is often used to blow away molten material and enhance the cutting process.
- Post-Processing: Once the cutting is complete, the finished parts may undergo additional processing, such as cleaning, deburring, or coating.
Types of Laser Cutting Technologies
CO2 Lasers
- Uses a mixture of carbon dioxide, helium, and nitrogen gases
- Suitable for non-metallic materials and low-reflectivity metals
- Wavelength of 10.6 microns
- Power range typically 25-100 watts (industrial grade can reach several kilowatts)
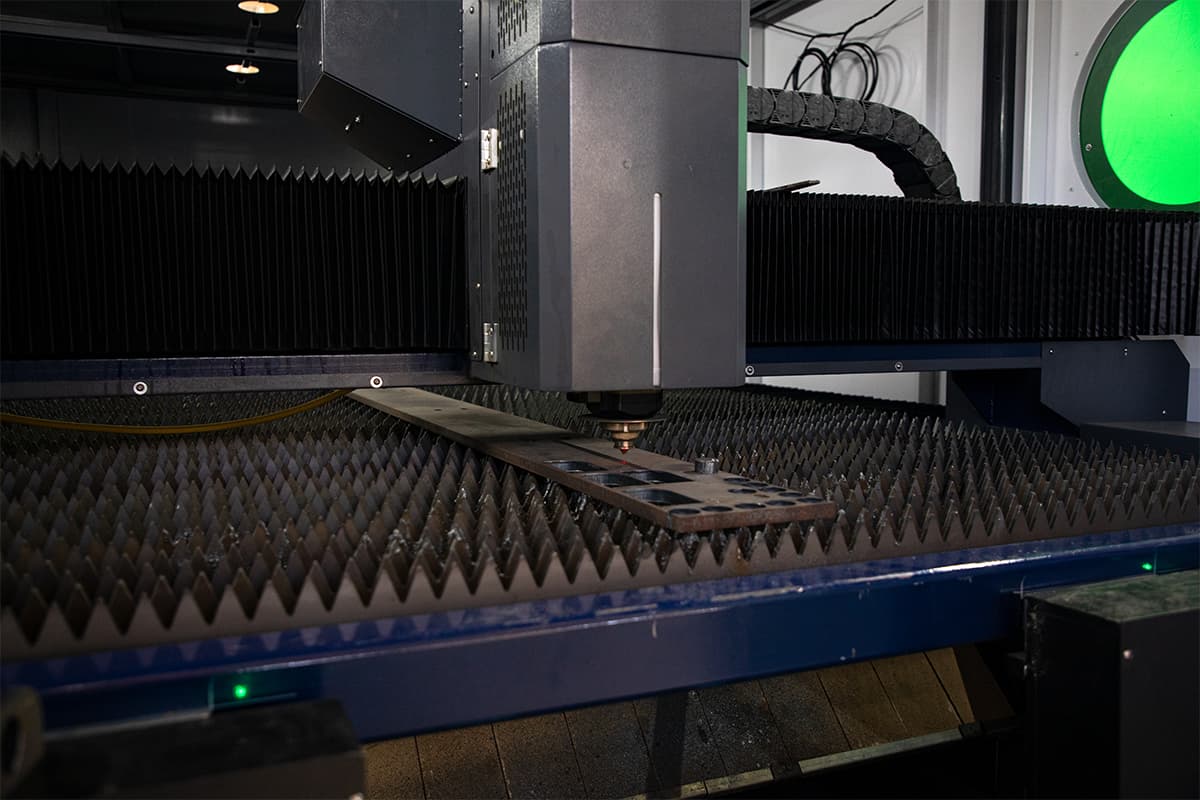
Fiber Lasers
- Uses optical fibers doped with rare earth elements (such as erbium or ytterbium)
- Particularly suitable for cutting high-reflectivity materials like aluminum and copper
- Wavelength of about 1.064 microns
- Can produce extremely small focal diameters, high cutting precision
- Low maintenance requirements, long service life (at least 25,000 hours)
Nd:YAG Lasers
- Uses neodymium-doped yttrium aluminum garnet crystals
- Suitable for high-precision applications such as marking and engraving
- Can cut metals and some non-metallic materials
III. Advantages of Laser Cutting
Laser-cutting technology offers numerous benefits that make it a preferred method in various manufacturing processes. Here are some of the key advantages:
1. High Precision and Accuracy
Laser cutting provides unparalleled precision, capable of achieving extremely tight tolerances. The focused laser beam can cut intricate and complex shapes with high accuracy, making it ideal for applications that require detailed and precise cuts. The typical tolerance range for laser cutting is between 0.003 mm to 0.006 mm, which is significantly higher than other cutting methods.
The precision of laser cutting depends not only on the laser itself but also on the accuracy of the motion system. Modern high-end laser cutting machines often use linear motors and optical scales, achieving positioning accuracies of up to ±0.001mm in some cases.

The precision of laser cutting enables the creation of highly complex and intricate designs that would be difficult or impossible to achieve with mechanical cutting tools. This makes laser cutting ideal for applications in jewelry making, architectural models, and custom fabrication.
2. Speed and Efficiency
Laser cutting is much faster than traditional cutting methods, especially when dealing with complex cuts. Its high-speed nature allows for quicker production cycles, reducing overall manufacturing time.
This efficiency translates to increased productivity and lower operational costs. Some high-power fiber laser cutting machines can achieve cutting speeds of over 100m/min when cutting thin sheets.
The speed of laser cutting, combined with minimal setup time and the ability to switch between different designs quickly, leads to significantly reduced production times. This increased efficiency can result in higher output and shorter customer lead times.
3. Automation and Repeatability
Modern laser cutting machines are highly automated and controlled by computer numerical control (CNC) systems. This automation ensures consistent results across large production runs, with each piece being an exact replica of the others.
The repeatability of laser cutting is a major advantage for mass production. CNC systems typically use CAD/CAM software for programming, which further enhances processing flexibility and efficiency.
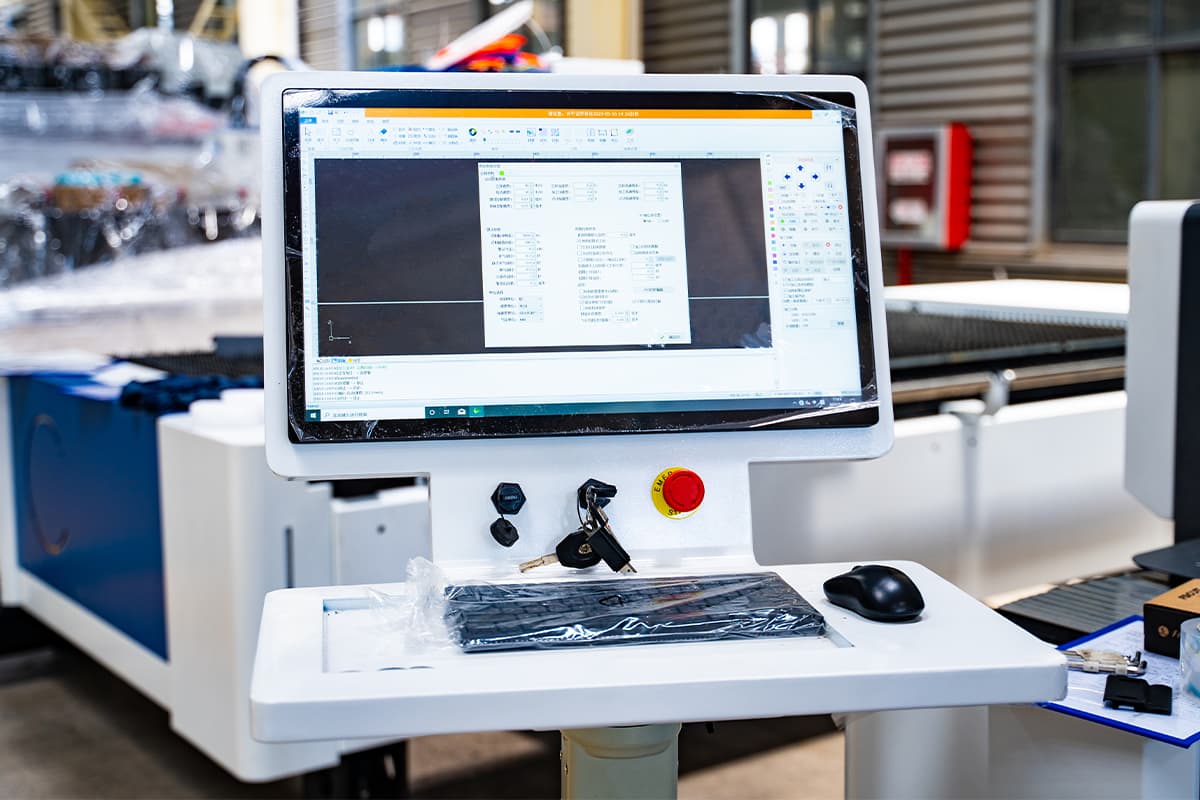
4. Clean and Contactless Process
Laser cutting is a non-contact process, meaning there is no physical contact between the cutting tool and the material. This eliminates the risk of contamination and reduces the wear and tear on the cutting equipment.
The result is a cleaner cutting process with minimal material deformation. Due to its non-contact nature, laser cutting is particularly suitable for processing fragile or easily deformed materials.
5. Material Versatility
One of the standout features of laser cutting is its ability to cut a wide range of materials, including metals, plastics, wood, ceramics, and more. Different types of lasers are indeed suitable for different materials, but the main distinction is between CO2 lasers and fiber lasers.
CO2 lasers are more suitable for non-metallic materials, while fiber lasers are better for metallic materials, enhancing the versatility of laser cutting technology.
6. Low Power Consumption
The energy efficiency of laser cutting depends on the specific application. For some complex cutting tasks, it may be more energy-efficient than traditional methods.
However, high-power laser cutting machines typically consume a lot of electricity, so overall energy efficiency needs to be considered.
7. Reduced Waste
Laser cutting is highly efficient in terms of material utilization. The precision of the cuts minimizes the amount of waste material, which is beneficial both economically and environmentally.
This efficiency helps in reducing the cost of raw materials and disposal. Laser cutting can also achieve multi-sheet nesting, further improving material utilization.
8. Safety
Laser cutting machines are designed with safety features that protect operators from harm. The automated nature of the process reduces the need for manual intervention, minimizing the risk of accidents.
Additionally, safety enclosures and proper ventilation systems help in managing any fumes or emissions produced during cutting.
Modern laser cutting machines are usually equipped with laser protective covers and interlocking devices that automatically cut off the laser when the protective cover is opened, further ensuring operational safety.
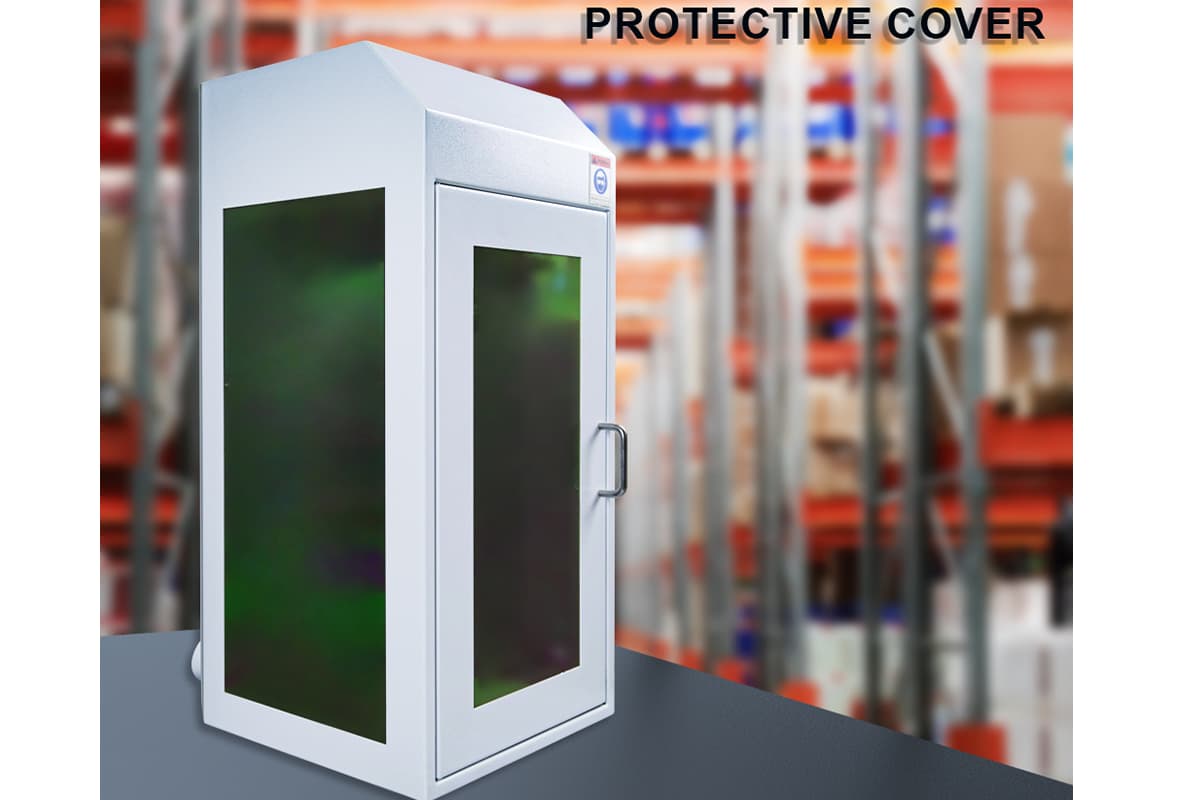
IV. Disadvantages of Laser Cutting
Despite its many advantages, laser cutting technology also has some drawbacks that need to be considered:
1. High Upfront Costs
The initial investment required for laser cutting machines can be substantial. High-quality laser cutters, especially those with advanced features and higher power, can be expensive. This cost can be a barrier for small businesses or those with limited budgets.
While the initial investment is high, the long-term cost-effectiveness should be considered. For high-volume production, the efficiency of laser cutting can offset the initial costs over time.
2. Material Limitations
Laser cutting is not suitable for all materials. Certain metals like copper and aluminum, which have high reflectivity, can be challenging to cut effectively. Copper and aluminum can be cut effectively with modern fiber lasers, though they require higher power and special techniques.
Additionally, there are limitations on the thickness of the materials that can be cut. Typically, laser cutting is more efficient for thinner materials, and cutting very thick materials can be slow and less effective.
Reflective materials can potentially damage the laser system if not handled correctly. Some materials, like PVC, should not be laser cut due to the release of toxic fumes.
3. Energy Consumption Variability
While laser cutting can be energy-efficient, the amount of energy consumed can vary depending on the material and its thickness. Cutting thicker materials or using high-powered lasers can lead to significant energy consumption, which can increase operational costs.
Modern laser cutting machines often incorporate energy-saving features like automatic standby modes to help mitigate high energy consumption during non-cutting periods.
4. Need for Technical Expertise
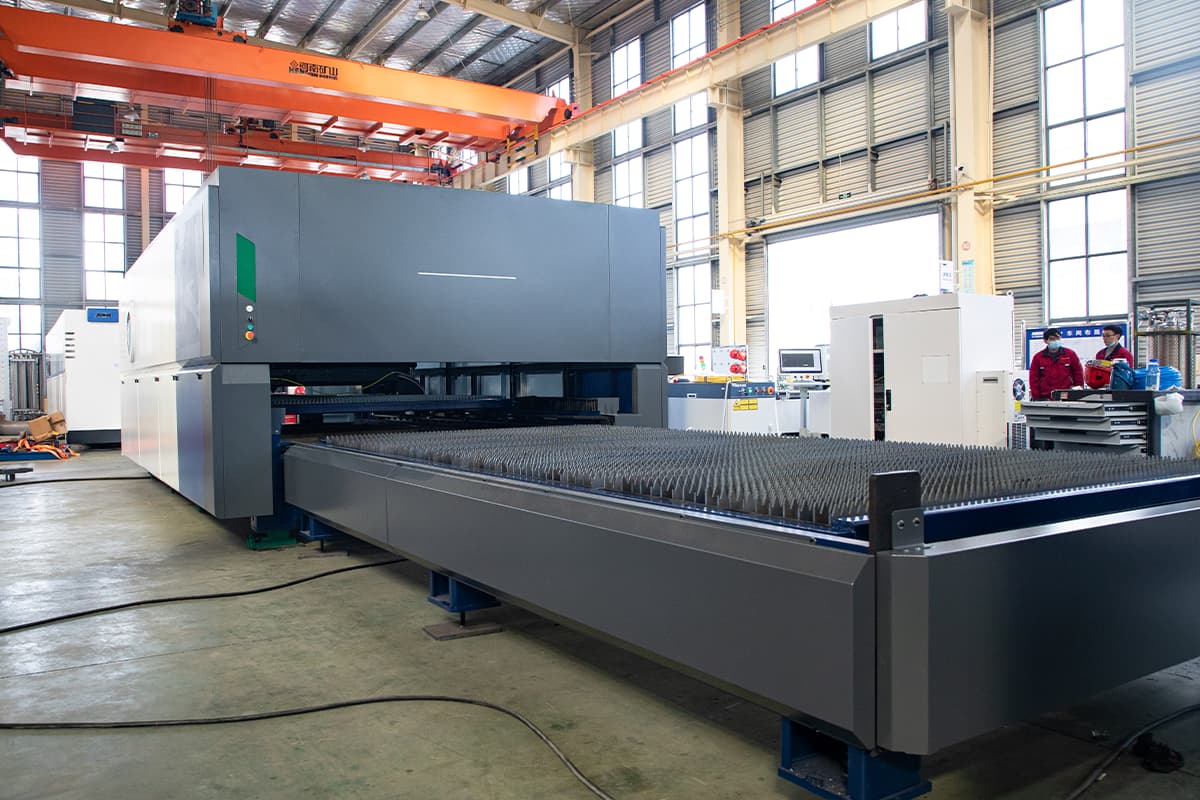
Operating and maintaining laser cutting machines requires skilled operators. Proper setup and calibration are crucial for achieving the desired cutting quality. The need for technical expertise can lead to additional labor costs and training expenses.
The increasing automation and user-friendly interfaces in modern laser cutting machines are helping to reduce the learning curve, though expert knowledge is still crucial for optimal performance.
5. Maintenance and Repair
Laser cutting machines require regular maintenance to ensure optimal performance. Parts such as lenses and mirrors may need frequent replacement, especially in high-usage environments. Maintenance and repair costs can be high, adding to the overall operational expenses.
Preventive maintenance schedules and proper operator training can help reduce unexpected downtime and extend the life of critical components.
6. Production Rate Variability
The production rate of laser cutting can vary based on the type of material and its thickness. While laser cutting is generally fast, some materials may slow down the process, affecting overall productivity. This variability needs to be managed to maintain efficient production schedules.
Advanced nesting software and cutting path optimization can help maximize efficiency and minimize production rate variability.
7. Health and Safety Concerns
Certain materials, when cut using a laser, can produce harmful fumes and gases. Proper ventilation and fume extraction systems are necessary to ensure a safe working environment.
Additionally, there is a risk of burns or injuries if the laser beam comes into direct contact with the skin, emphasizing the need for safety protocols and protective equipment.
The importance of proper laser safety training for all operators. Modern laser cutting machines often come with built-in safety features like automatic shut-off systems and enclosed cutting areas to minimize risks.
8. Thermal Effects
Laser cutting generates heat, which can cause thermal distortion in some materials, especially in thin sheets or near the edges of cut parts. This can lead to reduced accuracy or the need for post-processing in precision applications.
9. Limited 3D Cutting Capability
While laser cutting excels in 2D applications, its capability for true 3D cutting is limited compared to some other technologies like 5-axis waterjet cutting. This can be a disadvantage for certain complex 3D parts.
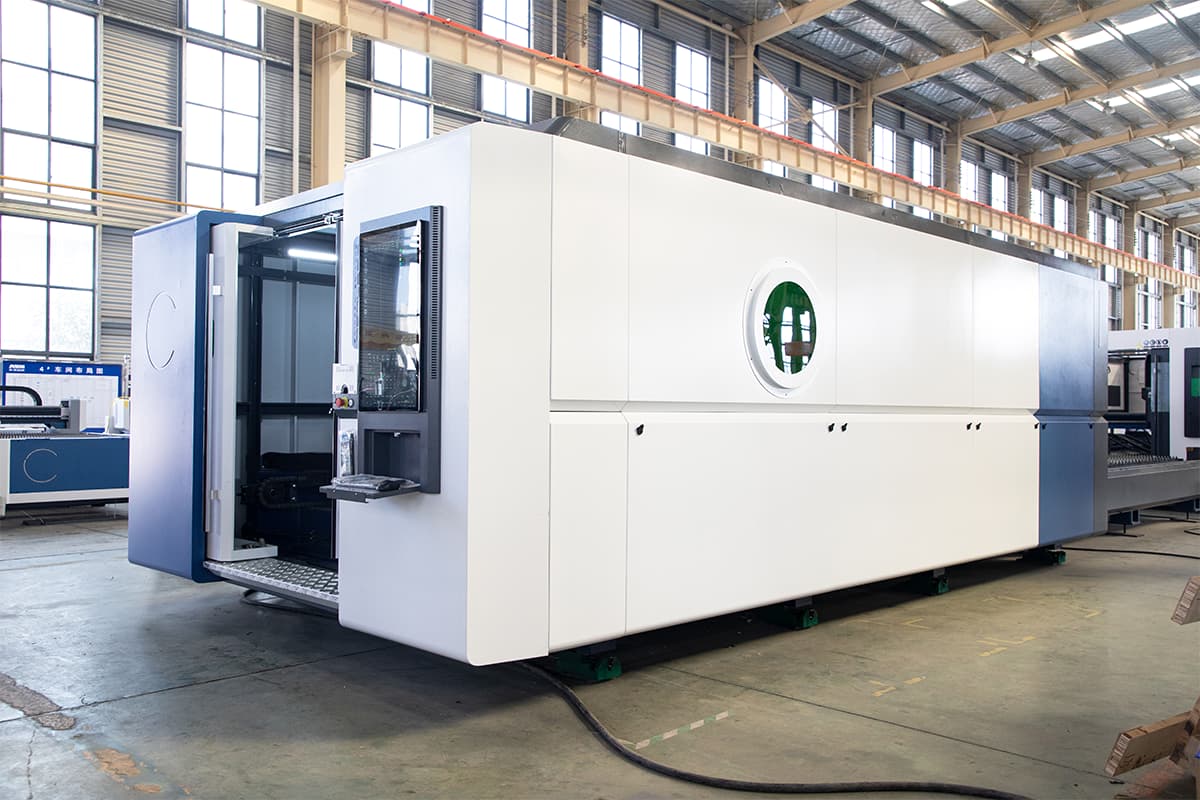
10. Size Limitations
Restricted cutting area: The size of the cutting bed limits the dimensions of the material that can be processed. While industrial-sized machines can handle large sheets, they are also more expensive and require more space.
Challenges with large-scale projects: For very large projects, multiple cuts and joining of pieces may be necessary, which can be time-consuming and may affect the overall quality of the final product.
V. Comparison with Other Cutting Methods
A. Laser Cutting vs. Water Jet Cutting
Aspect | Waterjet Cutting | Laser Cutting |
---|---|---|
Material Compatibility | Can cut more varied materials including thick, mixed materials | Primarily cuts thinner materials, metals, and plastics |
Heat Impact | No heat-affected zone (HAZ) | HAZ present, though minimal with modern lasers |
Precision | Lower than laser, due to wider cut path | Extremely precise cuts |
Speed | Slower, particularly on thicker materials | Faster, especially on thinner materials |
Material Distortion | No thermal distortion | Some thermal distortion possible |
Advantages | Can cut thicker materials; No heat-affected zone; Can cut a wider range of materials, including those unsuitable for laser cutting | Generally faster for thin materials; More precise for intricate designs; Often cleaner cuts with less need for finishing |
B. Laser Cutting vs. Plasma Cutting
Aspect | Plasma Cutting | Laser Cutting |
---|---|---|
Material Thickness | Better for thick materials | Better for thin to medium materials |
Precision | Lower precision, wider kerf | Higher precision, narrower kerf |
Speed | Faster in cutting thick materials | Faster in cutting thin materials |
Cost | Generally less expensive equipment | More expensive equipment |
Edge Quality | Rougher edges with potential dross | Cleaner edges with minimal dross |
Advantages | Can cut very thick metals; Generally lower equipment cost; Faster for thick materials | Much higher precision and smaller kerf width; Ability to cut non-conductive materials; Cleaner cuts with less dross |
C. Laser Cutting vs. Traditional Mechanical Cutting
Aspect | Traditional Cutting (CNC Machining) | Laser Cutting |
---|---|---|
Material Shape | Can create complex 3D geometries | Typically creates 2D profiles |
Efficiency | Tool changes and maintenance reduce efficiency | High efficiency for suitable materials |
Versatility | High versatility in material types | Best suited for specific material types |
Setup Time | Lengthier setup times for complex parts | Quick setup for repetitive jobs |
Material Waste | More waste due to cutting tool path | Less waste due to precision cutting |
Advantages | Often lower initial investment; Can be faster for simple, high-volume cuts; No heat-affected zone | Much greater flexibility in design; No tool wear or replacement; Ability to quickly switch between different designs without tooling changes |
VI. FAQs
1. What are the main benefits of laser cutting over traditional cutting methods?
Laser cutting offers several key benefits over traditional cutting methods, including higher precision, faster cutting speeds, and greater flexibility in terms of the materials that can be cut. Additionally, laser cutting is a non-contact process, which reduces the risk of material contamination and tool wear.
2. Are there any health risks associated with laser cutting?
Yes, there are potential health risks associated with laser cutting, primarily related to the fumes and gases that can be emitted when certain materials are cut. Proper ventilation and fume extraction systems are essential to mitigate these risks. Additionally, operators must follow safety protocols to avoid direct exposure to the laser beam, which can cause burns or other injuries.
3. How does laser cutting compare to plasma cutting in terms of efficiency?
Laser cutting generally offers higher precision and cleaner cuts compared to plasma cutting. It is also more efficient for cutting thinner materials and can handle a wider variety of materials. However, plasma cutting can be more effective for cutting thicker materials and is often faster for these applications. Both methods have their own advantages and are chosen based on specific project requirements.
4. What types of materials are best suited for laser cutting?
Laser cutting is versatile and can be used on a wide range of materials, including metals (such as steel, aluminum, and titanium), plastics, wood, acrylic, and ceramics. The specific type of laser (CO2, fiber, or Nd:YAG) and its power will determine the best materials for cutting.
5. Can laser cutting be used for mass production?
Yes, laser cutting is well-suited for mass production. Its high precision, speed, and repeatability make it ideal for producing large quantities of parts with consistent quality. The automation capabilities of laser cutting machines also reduce the need for manual intervention, further enhancing efficiency and productivity.
VII. Conclusion
In conclusion, laser cutting machines offer numerous advantages, such as high cutting precision, fast speed, and wide material adaptability. However, they also have some limitations, including high equipment costs and high skill requirements for operators. When choosing a laser cutting machine, it is essential to consider your production needs and budget comprehensively.
If you are looking for high-quality laser cutting equipment, why not check out ADH Machine Tool? We are a professional sheet metal production manufacturer with over 20 years of industry experience. Our fiber laser cutting machines are of exceptional quality and offer excellent value for money.
Whether you need small-batch production or large-scale manufacturing, we can provide suitable laser cutting solutions. Our team is dedicated to serving you, ensuring that your production efficiency and product quality are guaranteed.
Frequency Gear Oil Pump,Flow Cycloidal Gear Pump,Lower Unit Gear Oil Pump,Centrifugal Gear Pump
NINGBO JIECHENG ELECTROMECHANICAL CO.,LTD. , https://www.jiechengmechanical.com