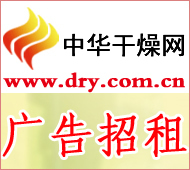
The main process parameters of the air drying equipment are the initial moisture content of the cut tobacco, the temperature of the drying air stream, and the amount of steam added in the drying air flow. Changing the settings of each process parameter will affect the processing quality of the cut tobacco.
Air drying equipment
The initial moisture content of the cut tobacco has an important influence on the filling value and the sensory quality after drying. Studies have shown that when the initial moisture content of the shredded tobacco is low, the filling value of the shredded tobacco treated with the air flow drying method is not much different from that of the drum dryer, and the weight of the single cigarette does not change significantly. However, with the increase of the initial moisture content (22% - 34%), the filling value of the shredded tobacco after drying is obviously increased. When the initial moisture content of the shredded tobacco further increases, the filling rate increases slowly. For the high-grade tobacco cut tobacco, with the increase of the initial moisture content of the cut tobacco, the aroma, fineness and concentration of the cigarette after air drying will decrease slightly, and the change of the miscellaneous gas, irritation and cleanliness will not be significant; and for the low-grade smoke formulation Tobacco shreds, with the increase of the initial moisture content of the cut tobacco, the aroma of the cigarette is slightly reduced, and the delicateness is reduced, but the miscellaneous gas, irritation and cleanliness are improved. Dry air temperature has a significant effect on the physical, sensory and chemical composition of cut tobacco. The temperature of the drying air flow was positively correlated with the filling value of the shredded tobacco after drying within a certain range. Studies have shown that the aroma and aroma of cigarettes are greatly affected by the temperature of the hot air. If the temperature of the hot air is too high, the aroma of the aroma will be reduced and the aroma will be reduced. According to Kim et al.'s study, drying vats of burley tobacco with superheated steam drying, the treatment temperature rose from 150°C to 320°C, and the filling value of cut tobacco also increased, from 6.08 cm3/g to 7.81 cm3/g. And with the increase of superheated steam temperature, the content of total sugar, nicotine and total amino acids in cut tobacco was significantly reduced, the content of total nitrogen and ether extracts was also reduced, and the sensory quality of burley tobacco also changed. Increased scent, irritation, bitterness, burning sensation and impact strength are reduced, and the aftertaste is improved. Dai Xiang and others conducted a test of the drying process of the tobacco in the draft of the tobacco-type cigarette. The results showed that the temperature of the airflow gradually increased from 200°C to 265°C. The sensory quality of cigarettes also gradually decreased, and the total sugar, total nitrogen and total alkaloids content in cut tobacco. Then fell.
When the hot gas stream is used to dry the cut tobacco, the steam is injected into the air before the heat exchanger, so that the heat transfer coefficient and the heat enthalpy can be increased, the drying rate can be accelerated, and the cut tobacco can be expanded. According to the research of Niansheng et al., the effect of the amount of steam applied in hot air on the internal quality of cigarettes is mainly reflected in the aroma characteristics and taste characteristics. Using a lower amount of steam injection improves the intrinsic quality of middle-to-high grade cigarettes. For the low-grade cigarettes, the higher amount of steam should be applied to the cut tobacco. Otherwise, the aroma quality, aroma and cleanliness of the cigarette will be reduced, and the dryness will increase.
The deepening of the research on the airflow drying technology is reflected in the research on the relationship between the process parameters of the airflow drying. Zhou Jun et al. demonstrated through experiments that under the premise of ensuring that the moisture content of the export tobacco is acceptable, other conditions remain unchanged. The process air temperature of HXD is directly proportional to the moisture content of cut tobacco and the flow of cut tobacco, which is inversely proportional to the amount of water added. During the production process, a reasonable and stable incoming cut tobacco flow rate and moisture content should be set first, and then the correct hot air temperature and hot air flow rate should be set, and the hot air temperature and the moisture content of the export cut tobacco should be adjusted by controlling the spray volume and the temperature of the cyclone separator. Zhang Dabo et al. conducted experiments by changing the operating parameters of HXD and statistically analyzed the collected data. It was concluded that the moisture content, material flow rate, process gas flow rate, and steam injection volume were independent variables, and the initial temperature of the air flow was the dependent variable. The regression equation can be used to calculate the combination of parameters that ensure the normal operation of the HXD so that the moisture content of the dried cut tobacco outlet can be evenly and stably achieved in a short time. Zhengzhou Tobacco Research Institute also conducted comparatively comprehensive experimental research on the main technical parameters of airflow drying such as initial moisture content, material flow rate, process gas flow rate, steam application amount and equipment operating conditions, product processing quality and intrinsic quality. The influence of many single factor parameter changes on the overall processing quality of cigarettes during the HXD work process.
News link:
The working principle of the air drying equipment is that the wet material enters the drying equipment through the conveyor and the heated natural air. At the same time, the entrained material in the swirl dryer enters from the tangential direction and forms a spiral movement along the inner wall. The material is evenly distributed in the air stream. Rotate and move and dry, and the dried product is discharged from the cyclone separator. A small part of the fly powder is recycled by the cyclone dust collector or bag filter. The wet, even agglomerated, material is then crushed by a blower until it disperses, stirring, mixing, and then parallel flow of the material and the hot gas stream during the dispersion process.
Plastic Mould,Thin Wall Container Box Mould,Thin Wall Container Box Fruit Molds,Plastic Injection Mould
Yuyao Hongzhou Plastic Technology Co., Ltd. , https://www.hongzhoumould.com