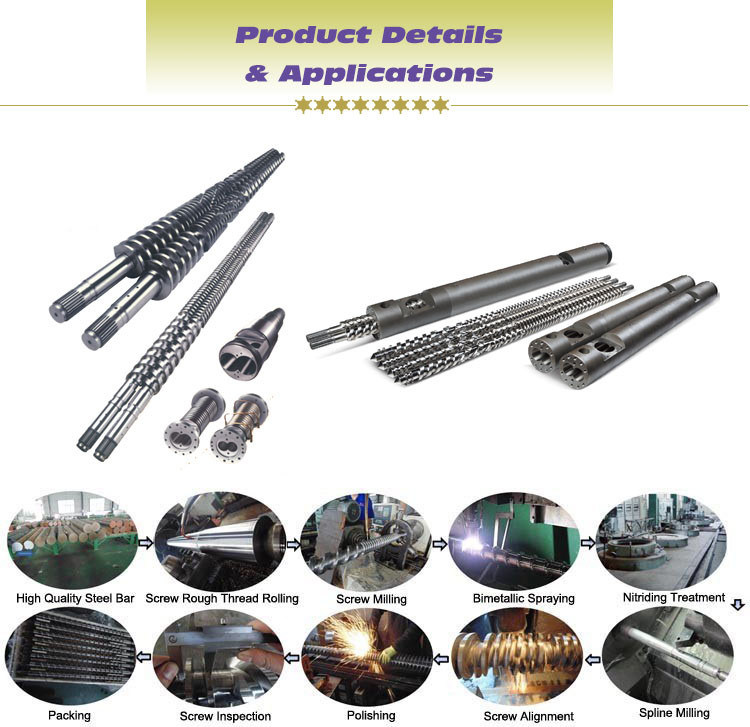
Technical Information for Conical Twin Screw Barrel | |||
Main Base materials | 1.38CrMoAlA (SACM645) | Main Alloy Materials | 1. Ni-based alloy/Deloro alloy |
2. SKD-61 (Special Tool Steel) | 2. Tungsten carbide/Wolfram carbide | ||
3. 42CrMo (Ultrahigh StrengthSteel) | 3. NiCo-based alloy | ||
4. DC53 (Cold WorkDie Steel) | 4. Fe-based alloy | ||
5. W6Mo5Cr4V2 (High-SpeedToolSteel) | 5. Co-based alloy | ||
Processing Technics | 1. Heat treatment | Technical parameters | Nitriding layer depth:0.5-0.8mm |
2. Quenching | Nitrided hardness:900-1000HV | ||
3. Nitriding treatment | Bimetallic layer depth:3 mm | ||
4. Bimetallic alloy welding for screw | Bimetallic hardness:57~69HRC | ||
5. Bimetallic alloy centrifugal casting for barrel | Hard-chrome plating hardness after nitriding:≥950HV | ||
6. Hard-chrome electroplating | Chrome-plating layer depth:0.03-0.09mm | ||
Linearity of screw:0.015mm | Surface roughness:Ra 0.4 |
The most common types of conical twin screw barrel extruder | |||
types of screw (d/D) | length of work(mm) | quantity ofextruder(kg/h) | speed of screw rotate(rpm) |
Φ35/77 | 810 | 40-70 | 5~50 |
Φ45/99 | 990 | 50-80 | 5~45 |
Φ51/105 | 1070 | 100-150 | 4~45 |
Φ51/105 | 1220 | 100-150 | 4~45 |
Φ55/110 | 1220 | 120-180 | 4~40 |
Φ60/125 | 1320 | 150-200 | 4~40 |
Φ65/120 | 1440 | 200-250 | 4~40 |
Φ65/132 | 1440 | 200-250 | 4~40 |
Φ70/140 | 1460 | 220-300 | 4~40 |
Φ75/150 | 1480 | 250-320 | 4~35 |
Φ80/143 | 1660 | 300-360 | 4~35 |
Φ80/156 | 1800 | 300-360 | 4~35 |
Φ90/184 | 2000 | 400-500 | 3~35 |
The most common types of parallel twin screw barrel extruder | ||||||
D35/5 | D45/2 | D50/2 | D60/2 | D65/2 | D70/2Â Â | D72/2 |
D75/2 | D80/2 | D85/2 | D90/2 | D93/2 | D100/2 | D105/2 |
D110/2 | D115/2 | D120/2 | D125/2 | D130/2 | D140/2 | D150/2 |
D160/2 | D170/2 | D180/2 | D190/2 | D200/2 | D200/2 | D250/2 |
Screw types:
Gradual change, chop, barrier, distributary, separate, air exhausting, pin, mixing and etc.
For good plasticizing effect, we have different design of screw barrel to meet customer's demand.
Specification :
Dia 20mm-250mm; L/D=15-45
Scope of Application:
1. Generally plastic material
2. Pipe/ Profile/ Sheet/Pelletizing
3. WPC, ABS, TPR, TPU, PMMA, C-PVC, UPVC, RPVC, PET, EVA, PU,PE etc
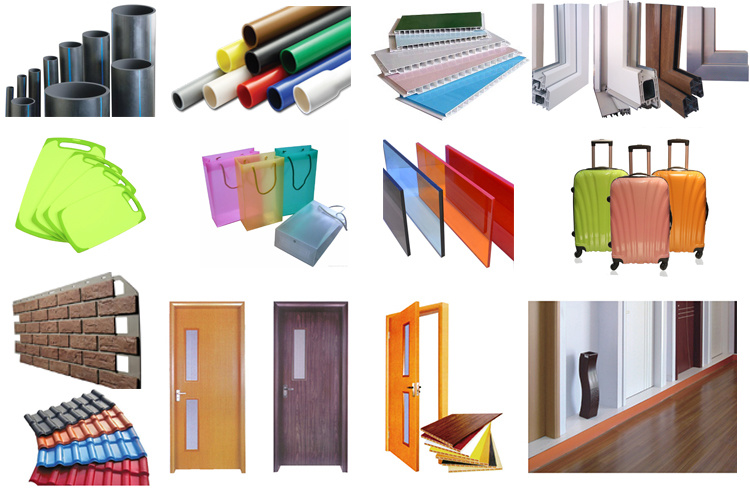
Treatment:
Nitrized, Chrome coating, Quenching, Bimetallic
We are foucs on each process to make sure each screw barrel is qualified according to technical requirement.Â
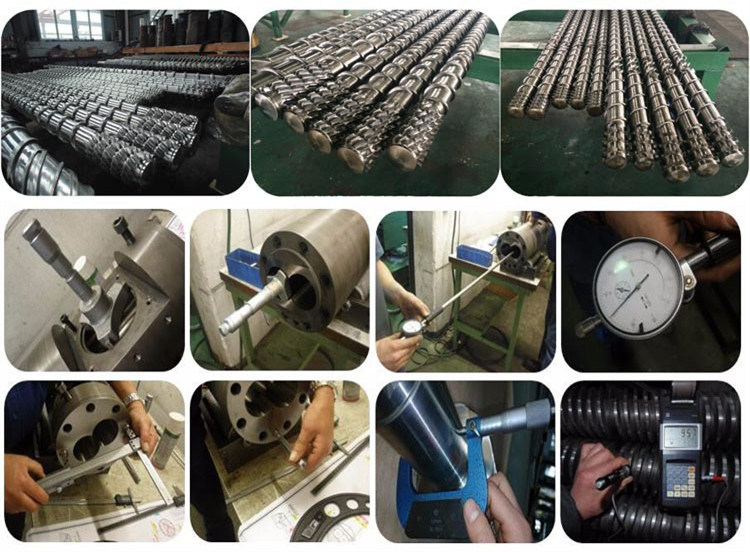
Packaging Details:
1. Be brushed anti-corrosive oil on extruder machine single screw.Â
2. Packed with film.Â
3. Packed in the AA wooden.
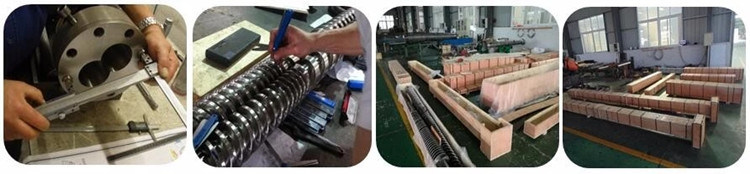
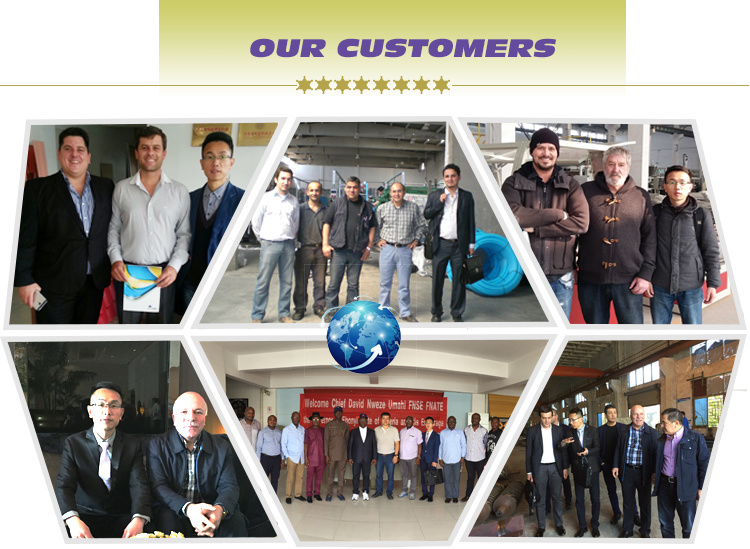
Please provide samples or requirements about dimensions and tolerances of , semi-finished and finished products, the equipment, the monthlly comsumption quantity, the current screw and barrel you are using, HRC and so on.
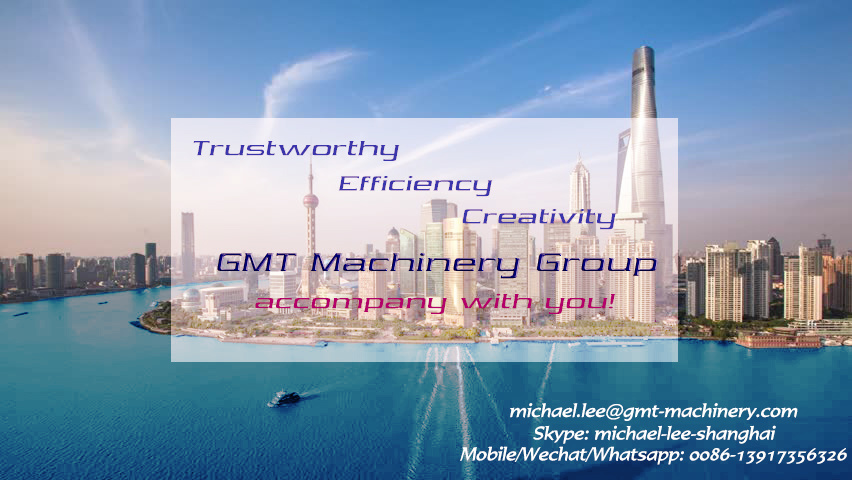
For more information, please kindly contact as below:
Mobile: 0086-13917356326
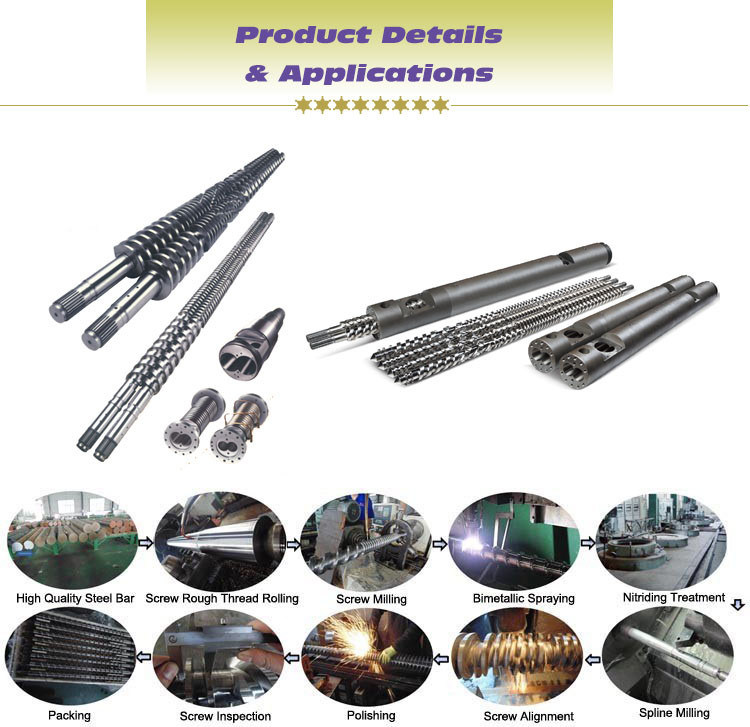
Technical Information for Conical Twin Screw Barrel | |||
Main Base materials | 1.38CrMoAlA (SACM645) | Main Alloy Materials | 1. Ni-based alloy/Deloro alloy |
2. SKD-61 (Special Tool Steel) | 2. Tungsten carbide/Wolfram carbide | ||
3. 42CrMo (Ultrahigh StrengthSteel) | 3. NiCo-based alloy | ||
4. DC53 (Cold WorkDie Steel) | 4. Fe-based alloy | ||
5. W6Mo5Cr4V2 (High-SpeedToolSteel) | 5. Co-based alloy | ||
Processing Technics | 1. Heat treatment | Technical parameters | Nitriding layer depth:0.5-0.8mm |
2. Quenching | Nitrided hardness:900-1000HV | ||
3. Nitriding treatment | Bimetallic layer depth:3 mm | ||
4. Bimetallic alloy welding for screw | Bimetallic hardness:57~69HRC | ||
5. Bimetallic alloy centrifugal casting for barrel | Hard-chrome plating hardness after nitriding:≥950HV | ||
6. Hard-chrome electroplating | Chrome-plating layer depth:0.03-0.09mm | ||
Linearity of screw:0.015mm | Surface roughness:Ra 0.4 |
The most common types of conical twin screw barrel extruder | |||
types of screw (d/D) | length of work(mm) | quantity ofextruder(kg/h) | speed of screw rotate(rpm) |
Φ35/77 | 810 | 40-70 | 5~50 |
Φ45/99 | 990 | 50-80 | 5~45 |
Φ51/105 | 1070 | 100-150 | 4~45 |
Φ51/105 | 1220 | 100-150 | 4~45 |
Φ55/110 | 1220 | 120-180 | 4~40 |
Φ60/125 | 1320 | 150-200 | 4~40 |
Φ65/120 | 1440 | 200-250 | 4~40 |
Φ65/132 | 1440 | 200-250 | 4~40 |
Φ70/140 | 1460 | 220-300 | 4~40 |
Φ75/150 | 1480 | 250-320 | 4~35 |
Φ80/143 | 1660 | 300-360 | 4~35 |
Φ80/156 | 1800 | 300-360 | 4~35 |
Φ90/184 | 2000 | 400-500 | 3~35 |
The most common types of parallel twin screw barrel extruder | ||||||
D35/5 | D45/2 | D50/2 | D60/2 | D65/2 | D70/2Â Â | D72/2 |
D75/2 | D80/2 | D85/2 | D90/2 | D93/2 | D100/2 | D105/2 |
D110/2 | D115/2 | D120/2 | D125/2 | D130/2 | D140/2 | D150/2 |
D160/2 | D170/2 | D180/2 | D190/2 | D200/2 | D200/2 | D250/2 |
Screw types:
Gradual change, chop, barrier, distributary, separate, air exhausting, pin, mixing and etc.
For good plasticizing effect, we have different design of screw barrel to meet customer's demand.
Specification :
Dia 20mm-250mm; L/D=15-45
Scope of Application:
1. Generally plastic material
2. Pipe/ Profile/ Sheet/Pelletizing
3. WPC, ABS, TPR, TPU, PMMA, C-PVC, UPVC, RPVC, PET, EVA, PU,PE etc
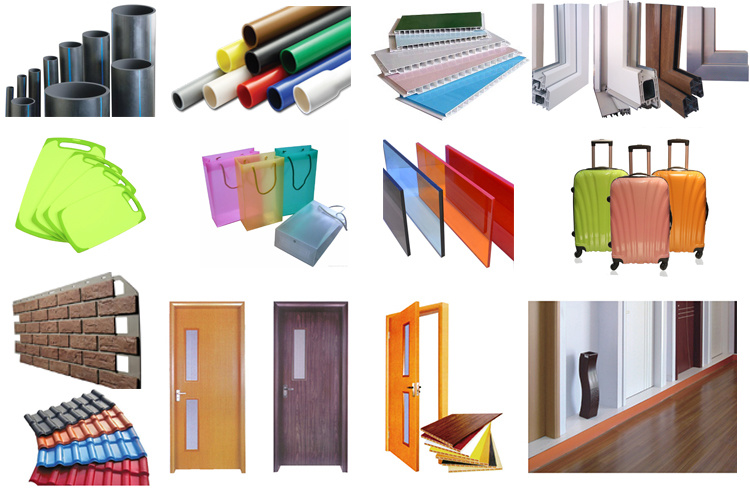
Treatment:
Nitrized, Chrome coating, Quenching, Bimetallic
We are foucs on each process to make sure each screw barrel is qualified according to technical requirement.Â
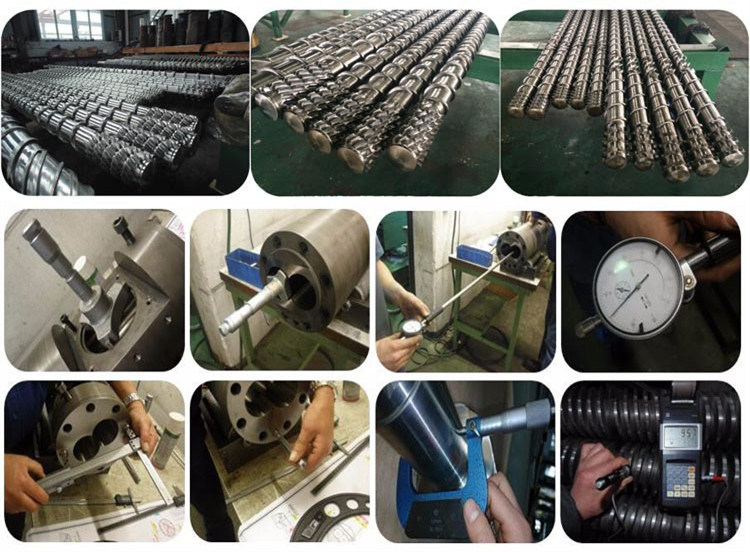
Packaging Details:
1. Be brushed anti-corrosive oil on extruder machine single screw.Â
2. Packed with film.Â
3. Packed in the AA wooden.
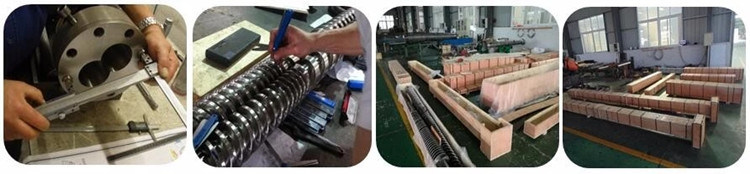
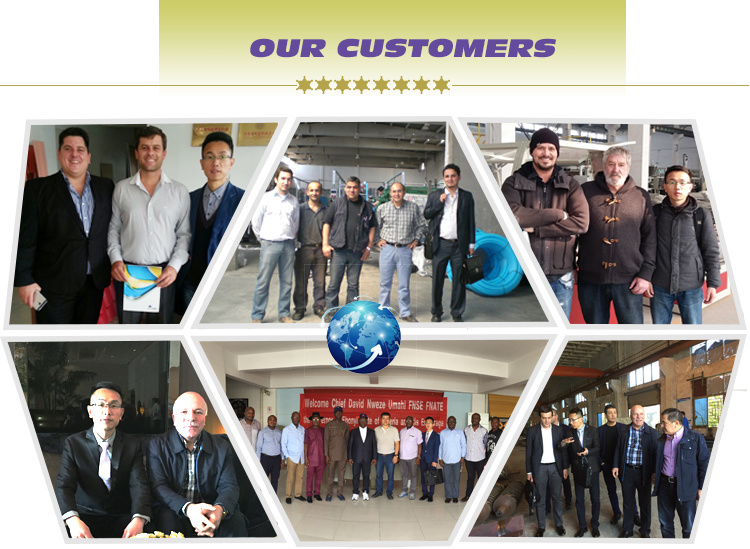
Please provide samples or requirements about dimensions and tolerances of , semi-finished and finished products, the equipment, the monthlly comsumption quantity, the current screw and barrel you are using, HRC and so on.
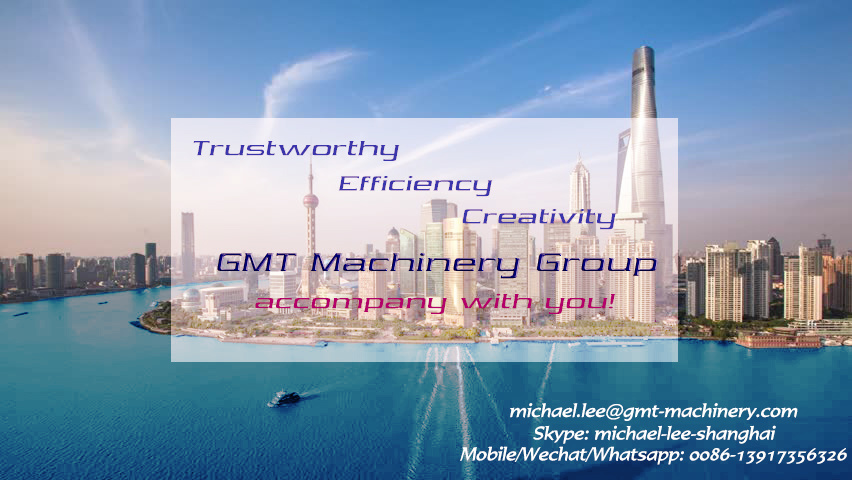
For more information, please kindly contact as below:
Mobile: 0086-13917356326
This series of equipment can regenerate various types of activated carbon such as coal, wood, nut shell, mineral (petroleum), or powder, granule, column, or primary, extruded, and re-formed activated carbon, according to the characteristics of activated carbon fire method regeneration treatment , This series of equipment is equipped with unique flue gas treatment equipment to ensure the green and environmental protection of the activated carbon fire method regeneration process.
The device has the following characteristics:
1.Wide application field: the device can regenate various types of activated carbonon by adjusting the angle and rotational speed of furnace pipe.
2.Regeneration activated carbon in the oven retention time 40 minutes, which is applicable to the regeneration levelofall kinds of grain particles, for coal activated carbon also has good regeneration effect.
3.High degree of automation:the device operation achieves automatic control,with man-machine interface+Intelligent instrument control,reduces the operating workers and the labor intensity is low.
4.High recovery rate of Iodine value:basically returned to a new carbon levels above 90%.
5.Low carbon loss:≤1-2%(Coal carbon)But slightly higher than the JHR-O series activated carbon fuel diesel reclamation equipment
6.Easy installation, covers an area slightly larger, but the small space height requirements, large installed power.
Long service life:The core components furnace tube using thick wall (10 mm thick) 1200 ℃ high temperature resistance, corrosion resistant special stainless steel pipe.
Carbon Regeneration Kiln,Rotary Kiln Services,Carbon Regeneration Process,Chemical Regeneration Of Activated Carbon
Changchun Gold Research Institute Co.LTD , https://www.ccgoldmachinery.com