8.1 Check Valve Overview and Parameters 8.1.1 Check Valve Overview 8.1.1.1 Check valve, also known as check valve or check valve, is widely used in various types of pump outlet pipe, extraction pipe, hydrophobic pipes, and other not On the pipe that allows media to flow backwards. Check valve is the use of the valve before the valve pressure difference between the opening and closing of the valve automatically, its role is to make the media only one direction of flow, and to prevent its reverse flow. According to the different structure, the check valve can be divided into lifting (jumping heart type) and swing-type (rocking board type) two. Lift check valve must be installed in the horizontal pipe, and the valve flap axis perpendicular to the horizontal plane, in order to ensure the flexible flap movements and reliable work. Swing check valve as long as the valve flap to ensure that the pivot is horizontal, you can install any horizontal, vertical or inclined pipe. 8.1.2 Check valve main performance parameters 8.1.2.1 Reheater inlet pipe check valve on the right, size: PN4.65 DN 850. 8.2 check valve repair steps, process methods and quality standards 8.2.1 Check valve repair 8.2.1.1 Preparation 8.2.1.1.1 confirmed in the valve cavity and connected to the pipeline work, there is no pressure medium. 8.2.1.1.2 ready to dismantle the valve place to prevent damage to parts stacked. 8.2.1.1.3 Prepare necessary mapping equipment. 8.2.2 check valve repair steps, process methods 8.2.2.1 valve disassembly 8.2.2.1.1 release cover nut, remove the cover. 8.2.2.1.2 Remove the six-ring ring. 8.2.2.1.3 Using a special tool to lift the valve cover out of the valve body, remove the packing pressure ring. 8.2.2.1.4 Remove the hexagonal ring. 8.2.2.1.5 Use a special tool to lift the bonnet out of the valve body and remove the packing pressure ring. 8.2.2.1.6 lift the valve flap can be removed directly, check the spool and valve seat surface to determine the repair method. 8.2.2.1.7 On the screw-on disc, take off the fixing pin of the connecting frame and then remove the valve disc from the connecting frame to check the contact surface. 8.2.2.1.8 The valve cover, posted a good seal. 8.2.2.2 Inspection and Repair: 8.2.2.2.1 Check the valve body parts should be no blisters, cracks and corrosion corrosion defects, found should be repaired welding. 8.2.2.2.2 Sealing surface of valve seat should be ground manually or mechanically to eliminate its surface grooves and pits so that the sealing surface meets the specified quality requirements. 8.2.2.2.3 Disc seal surface defects available flat grinding, emery cloth grinding and other methods to eliminate, if the more serious flaws can be sent to the lathe light, the right research. 8.2.2.2.4 valve cover to clean, remove the body of the sealing packing, the packing rings and polished everywhere, check the valve cover seal body gap to meet the requirements, enhance the nut should ensure that the threaded part of the intact, the nut flexible and easy to use . 8.2.2.2.5 Repair six-ring, surface smooth and slot clearance meet the requirements, or should be processed. 8.2.2.2.6 valve lift valve, valve disc and positioning sleeve all polished clean, remove rust scale, the test is flexible. 8.2.2.2.7 Swing check valve, the fixed pin should be complete and straight. Reliable connection with the fixed end. Vertical range of freedom to lift and fall, the shaft end should not have jamming phenomenon. 8.2.2.3 Check valve assembly 8.2.2.3.1 Valve will be placed in the valve body, the rotary valve will be on the valve flap and connecting frame pin with a reliable connection, and then the connecting frame and valve body fixed end Shaft connection. 8.2.2.3.2 Put the valve cover into the valve body and fill in the sealing pressure as required. 8.2.2.3.2 packing pressure ring cover in the bonnet sealing parts, the packing pressure is good. 8.2.2.3.4 Six-ring sub-assembly All parts of the uniform gap, and then with the ring off. 8.2.2.3.5 Replacing the cover plate on the hexagonal ring, tighten the nut on the cover, so that the self-sealing packing pressed. 8.2.2.3.6 clean the valve and the surrounding area. 8.2.2.3.7 The operation personnel shall check the civilized environment of the equipment and finish the work ticket after the acceptance is passed. 8.2.2.3.5 together with the boiler hydrostatic test, check the packing roots without water, as qualified. 8.2.3 check valve overhaul quality standards 8.2.3.1 valve body clean, no rust and corrosion erosion. Smooth entrance without debris. 8.2.3.2 Flapper and valve seat sealing surface should be no pit, groove and corrosion, sealing surface full circle light, the surface finish below, the width of the contact surface should be more than 2/3 of the full mouth width. 8.2.3.3 Bolt Threaded Part is intact, there is no broken buckle and bite buckle phenomenon. The nut should be flexible. Hand should be screwed to the bottom of the bolt buckle. The combination should be coated with graphite powder. 8.2.3.4 Each ring block should be completely clean, no deformation, flexible into the slot, the gap between the upper and lower sides of the slot is 0.5mm, the height of the hexagonal ring into the slot should be the same. 8.2.3.5 Open the valve disc vertically up and down, the upper part should be flexible with the guide sleeve, no jam, the gap is 0.3-0.5mm. 8.2.3.6 Swing check valve Its valve flap and the fixed end of the connection should be flexible and reliable, lifting the valve flap by gravity should be able to fall freely, and the valve seat sealing surface sealed intact, no visible gaps. 8.2.3.7 Filler used should meet the requirements of the working medium. Sealed packing should ensure that the total height of the packing rings into the bonnet seal body should be flexible, no jam as to ensure that the packing of the packing effect. The replacement of the sealing filler, the interface should be cut into a beveled angle 45, each ring interface should be staggered 90-120, cutting filler length should be appropriate, into the filler indoor interface without gaps or superimposed phenomenon. 8.3 Safety, Health and Environmental Requirements 8.3.1 Safety 8.3.1.1 Check the safety measures and work flow first before meeting the safety rules and regulations before starting work. 8.3.1.2 Before loosening the valve bolt, check that there is no pressure in the pipeline, check if the drain door is opened and the water is released. 8.3.1.3 In the course of maintenance, the hydrophobic door must be kept open until the valve does not leak out of the wound. 8.3.1.4 When loosening the bolts, care shall be taken to prevent the possibility of being sprayed by steam or hot water that may accumulate. 8.3.1.5 After the valve is disassembled, clean the tools and the removed parts, and take protective measures on the removed valve to prevent foreign matter from falling in. 8.3.1.6 When working on soda pipe for a long time, the pipe section with tail shall be reliably cut off by the block pipe with tail in the overhaul section. 8.3.1.7 During the installation and re-installation of pipe flanges or valves, do not allow your fingers to touch the hole. To prevent finger injury. 8.3.1.8 Working at heights, wear safety helmets, wear protective clothing and work shoes, and take good care of them. Materials, spare parts, etc. should be placed in a solid and reliable place. 8.3.1.9 In case of emergency elimination, safety measures such as anti-scald work clothes, gloves, work shoes and the like shall be taken to prevent scalding by high-temperature valve pipes. 8.3.1.10 The use of electric tools to pay attention to leakage, the risk of electric shock, the use of electric grinding, the risk of eye damage with iron filings; check the power tools to prevent leakage, the use of angle grinders and other power tools to wear protective eyes. 8.3.1.11 Replacing the valve During welding, prevent electric sparks from splashing in the cable tray causing a fire hazard. 8.3.2 Health 8.3.2.1 In the work environment under the conditions of high temperature work, we must take measures to prevent heat stroke. 8.3.2.2 on the workplace near the high-temperature objects, to be protected, to prevent staff access to hot objects. 8.3.2.3 Do not use excessive force in the work to prevent waist sprain. 8.3.2.4 Use dust masks or qualified masks when removing insulation from pipes or valves. 8.3.2.5 Workers entering the pipeline or underground shall rotate their work and rest. 8.3.3 Environment 8.3.3.1 Remove the parts to be neatly arranged. 8.3.3.2 Valve Tightness Test Used kerosene should be properly placed and not be directly dumped into the garbage dump or sewer. 8.3.3.3 When painting pipes or valves, work to prevent the paint from falling to the ground or to other equipment. 8.3.3.4 After the work is over, clean the work site and keep the workplace clean. 8.3.3.5 work is completed, clean up the site, classified into garbage dumps. 8.4 After-service test items and standards 8.4.1 equipment before operation, with the furnace pressure. Check the packing roots have water seepage, the valve opens check the pipe outlet media out, no media after the closure of the phenomenon of drip, indicating that the valve sealing surface qualified, packing appropriate. 8.5 Maintenance category and overhaul cycle 8.5.1 Maintenance once a year, the size of a random set of equipment repair line 8.6 Check valve maintenance 8.6.1 Maintenance in routine operation 8.6.1.1 Cruise inspection content 8.6.1.1.1 Visual inspection or listen to the boiler Is there a leak in the valve? Is the valve damaged? 8.6.1.2 Patrol inspection 8.6.1.2.1 Visual inspection or hearing of the boiler valve sealing surface without? B leakage, parts without damage. 8.7. Routine Maintenance Items, Cycles, and Standards Periodic Maintenance Items Cycle Standard Grease 3 months Apply to stem threads and grease cup Fill appropriate amount RYKon P2
Car Grill
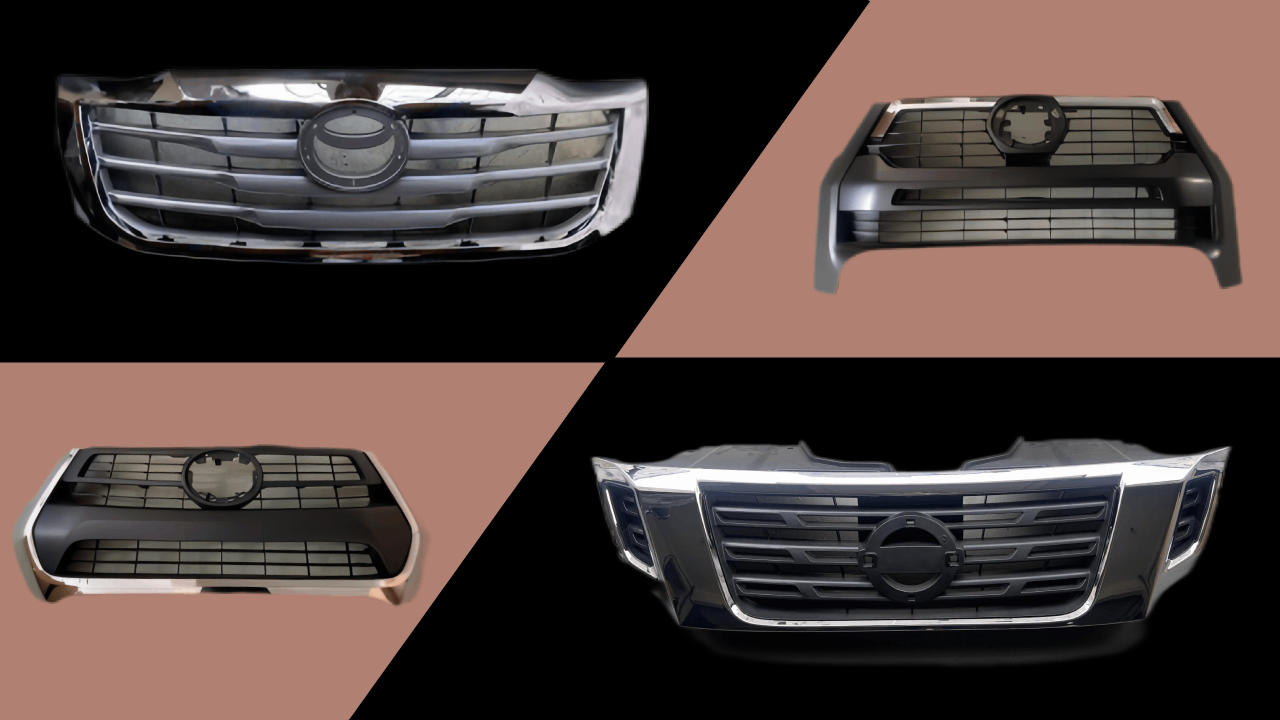
We have years of experience in the production of automotive parts and have a domestically leading fully automatic melting and die-casting production line. We have arranged multiple lean CNC machining production lines and are equipped with first-class inspection and testing equipment. We meticulously create excellent quality products to serve customers.
The car grille is not just a net, but a key component that links the hood, Front Bumper, and left and right headlights. Its main function is to provide air intake and ventilation for the water tank, engine, air conditioning, etc., and also has a certain protective effect.
We are committed to providing you with reliable and satisfactory car grilles, which not only have practical functions but also meet your aesthetic needs for your car. Click below to browse our car grille related products.
Related Suggestions: Car Grill, Custom Distinctive Car Grilles, Custom Big Car Grills, Toyota Car Grill Protector, Custom Car Grille Guard, Car Grill Mesh Black
Car Grill,Custom Distinctive Car Grilles,Custom Big Car Grills,Toyota Car Grill Protector,Custom Car Grille Guard,Car Grill Mesh Black
Danyang Hongwen Vehicle Industry Co., Ltd. , https://www.cn-hosc.com